Unsere
Leistungen
Lösungen, die passen wie ein Maßanzug.
Entwickelt mit AX Intelligence.
Finden Sie in unserer Leistungsübersicht realisierte Projekte und lassen Sie sich inspirieren. Ob Werkzeugmaschinen, Produktionsmaschinen, Fertigungslinien oder Sondermaschinen. Entdecken Sie konkrete Beispiele, die bereits erfolgreich umgesetzt wurden, und lassen Sie sich inspirieren, wie auch Ihre Produktion von unserem innovativen Designprozess AX Intelligence profitieren kann.
Mit AX Intelligence erhalten Sie Automatisierungslösungen, die passen wie ein Maßanzug.
Werkzeugmaschinen
Schleifmaschine
mit Multifunktionscontainer
Leitsatz: Nutzen sie das volle Potential ihrer Produktion
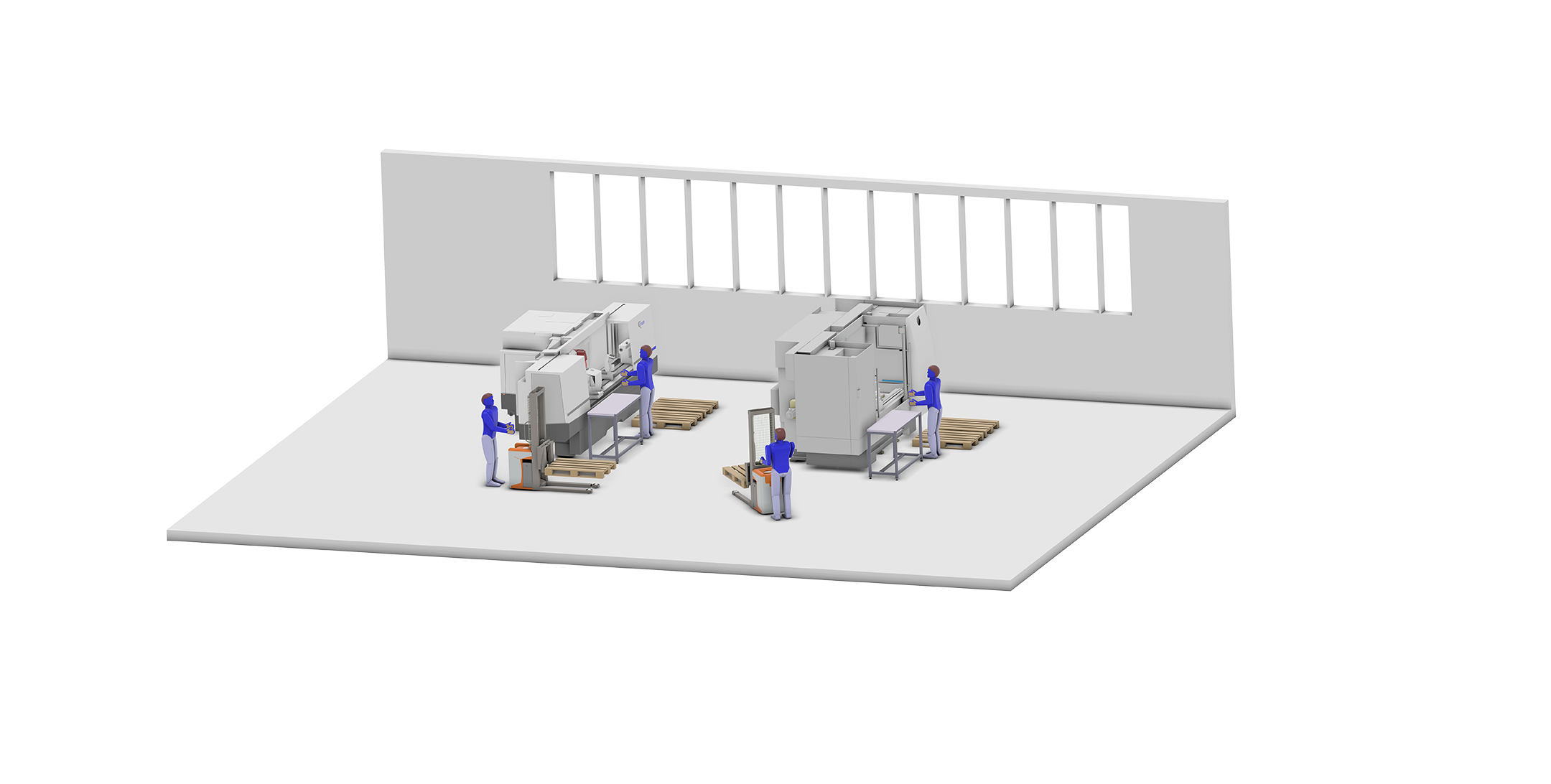
Vorher – manuelles Bauteilrüsten der Schleifmaschine
- Halbfertigteile werden in Holztrays per Europalette an der Schleifmaschine abgelegt
- manuelles Beladen der unterschiedlichen Halbfertigteilevarianten in die Schleifmaschine
- CAM-Programm Auswahl durch Bediener anhand Artikellaufzettel auf Palette
- Ablegen der Fertigteile in Holztrays und Transport zum Warenausgang
- je Bauteilvarianten unterschiedliche Holztrays teilweise zu wenig Holztrays für Losgröße vorhanden
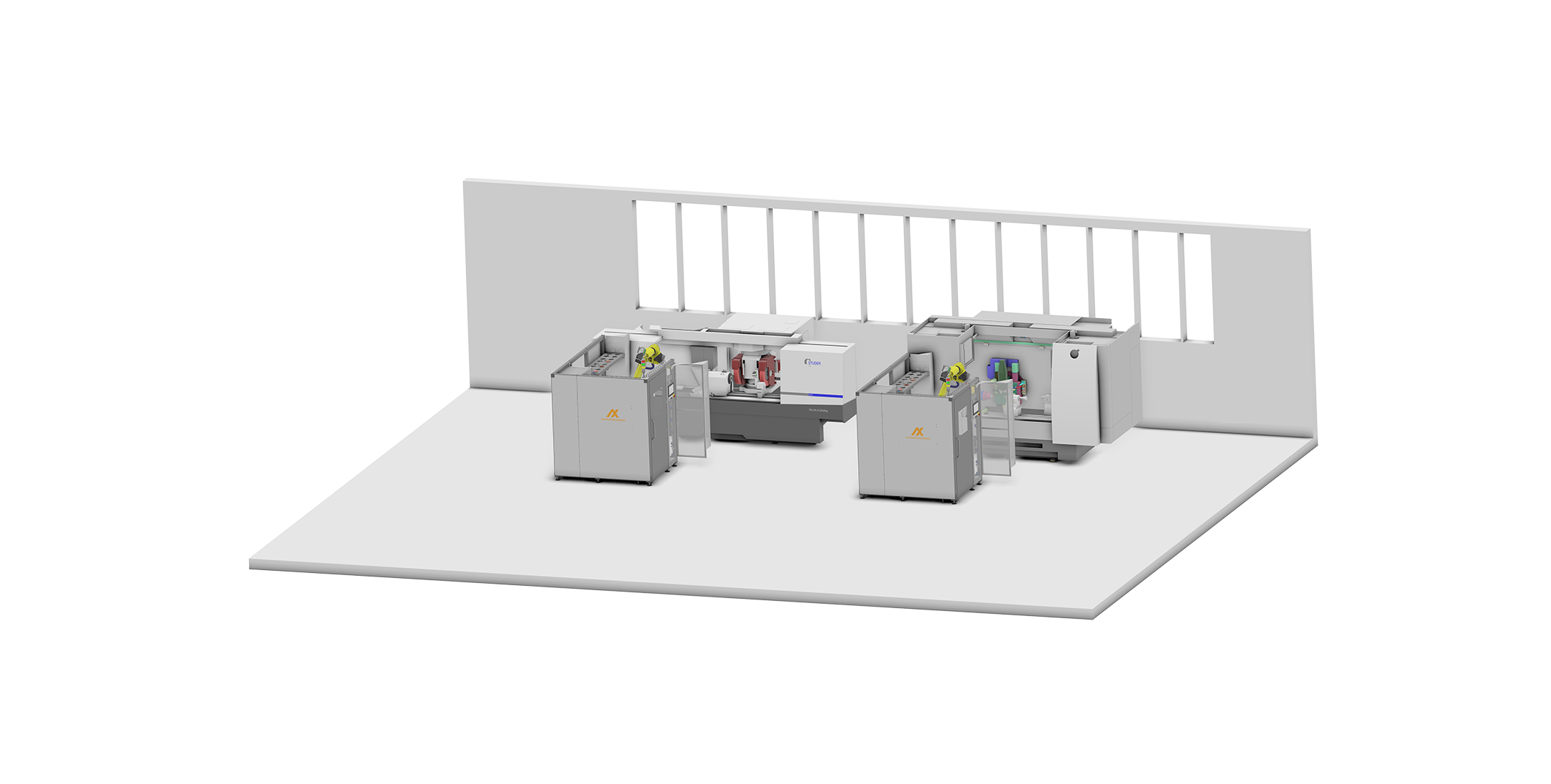
Nachher – smarte Be- und Entladung der Schleifmaschine
- aus dem Vorprozess werden Bauteile direkt in den Multifunktionscontainer gelegt
- Halbfertigteile werden im flexiblen Container an die Schleifmaschine geliefert
- je Schublade können unterschiedliche Bauteile in unterschiedlichen Losgrößen roboterentnahmegerecht positioniert werden
- jede Bauteilvariante kann durch einen individuellen Einsatz in der Schublade fixiert werden
- die Jobübergabe bzw. NC-Programmauswahl erfolgt automatisch nach dem Abstellen des Containers in der Zelle
- die Fertigteile werden in den universellen Einsatz zurückgelegt und der Status des Bauteils der übergeordneten Steuerung übergeben
- nach Abarbeitung des Containers erfolgt vom Bediener der Containerwechsel
- geschliffene Bauteile verbleiben im Container und werden dem nächsten Prozess z.B. Waschanlage roboterentnahmegerecht zur Verfügung gestellt
Dreh- und Fräszentren
mit Multifunktionscontainer
Leitsatz: ganzheitliche Betrachtung - von der Säge bis zur Auslieferung
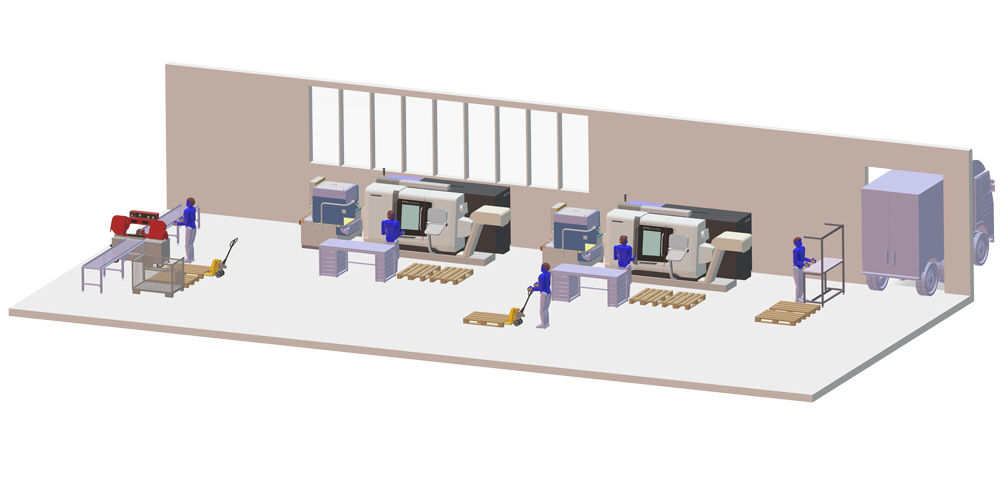
Vorher – manuelles Bauteilrüsten der CNC-Maschinen
- Rohmaterial wird an Bandsäge zugeschnitten und auf Europalette abgelegt
- Logistik transportiert Rohteile zur Bearbeitungsmaschine und stellt Palette vor CNC-Maschine ab
- manuelles Beladen der unterschiedlichen Rohteilvarianten in CNC-Maschine
- CAM-Programm Auswahl durch Bediener anhand Artikellaufzettel auf Palette
- ablegen Fertigteile auf Europalette und Transport zum Warenausgang
- Rohteilgewicht bis zu 20kg / Aussen Ø20-Ø320mm / 4.000 Bauteilvarianten / Kleinserienfertigung
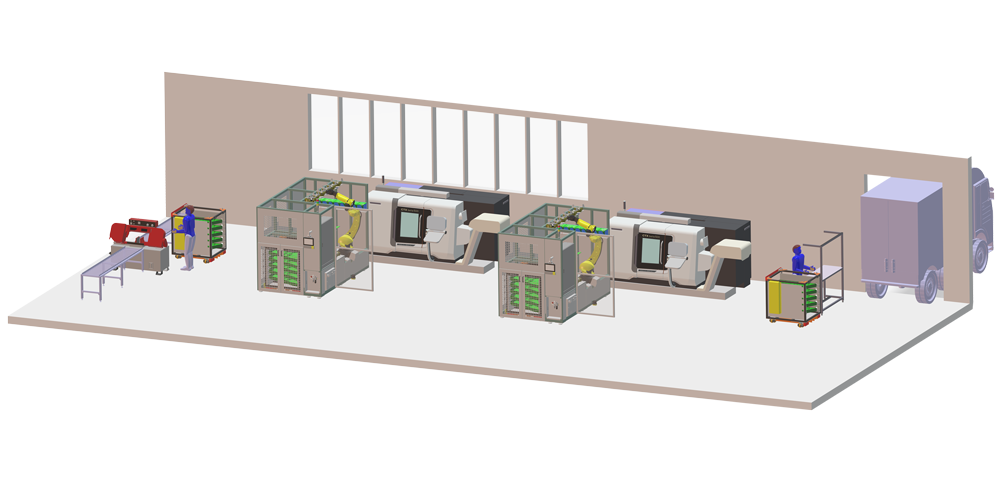
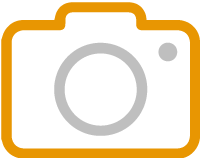
Nachher – effiziente CNC Be- und Entladezentren mit Multifunktionscontainer
- Rohmaterialzuschnitt wird an der Säge nach Fertigungsplanung im Container eingelegt
- Status wird an das übergeordnete Leitsystem übertragen und an RFID-Chip am Container gespeichert
- in den mehrlagigen Containerschubladen werden die Rohteile zentriert und fixiert
- Container wird zur Bearbeitungsmaschine bewegt und dort automatisch in Anlage fixiert – Fertigungsauftrag wird ausgelesen
- Rohteile werden aus den einzelnen Schubladen über Robotik entnommen und dem Maschinenspannfutter übergeben
- die Übertragung des CAM-Programms erfolgt nach Fertigungsauftrag aus der CAM-Bibliothek
- die Fertigteile werden durch die Robotik in die Containerschubladen zurückgelegt
- Greiferwechsel am Roboter je nach AussenØ erfolgt automatisch über Fertigungsauftrag
- die Containertechnik unterstützt mit ihrer definierten Bauteillage und dem gespeicherten Fertigungsauftragsstatus auch die nachfolgenden Arbeitsprozesse
➜ Die Containertechnik ist bereits für die Nachrüstung eines fahrerlosen Transportsystems, konzipiert.
5-Achs Universal-Bearbeitungszentrum
vom Schüttgut in die Bearbeitung
Leitsatz: Wir erweitern den Horizont für großartige Lösungen
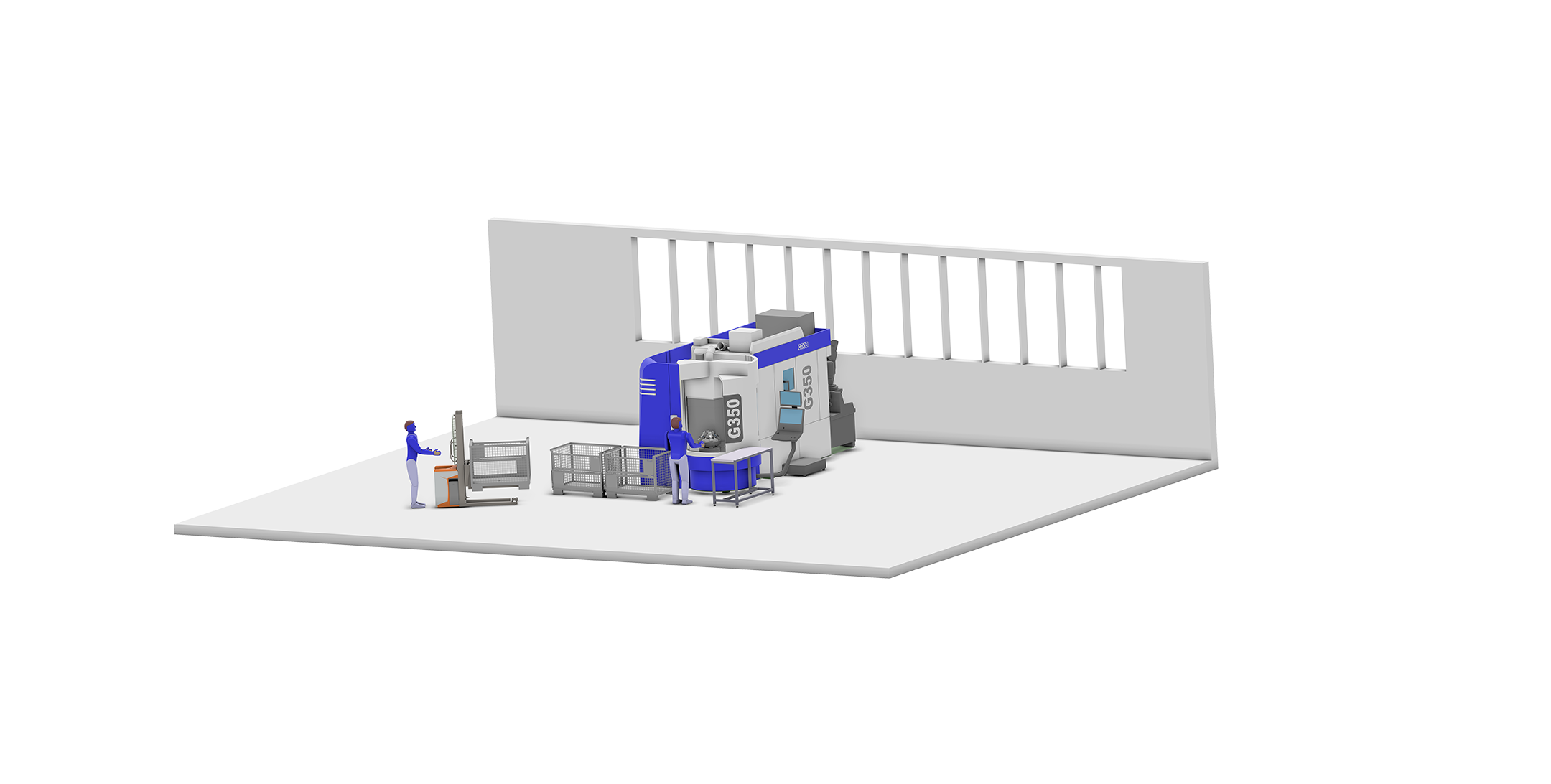
Vorher – manuelles Bauteilrüsten aus Schüttgut
- Schüttgutbehälter mit 4Stk Gusssteilvarianten wird an die Anlage gestellt
- Mitarbeiter entnimmt Bauteile aus Behälter und bestückt Anlage je nach Spannmatrizentype
- CAM-Programm Auswahl durch Bediener
- nach OP10 legt der Mitarbeiter die Teile wieder in die Box, diese werden einem externen Zwischenprozess zugeführt
- nach dem Zwischenprozess erfolgt die OP20 Bearbeitung, hierzu entnimmt der Mitarbeiter die Bauteile aus der Box und bestückt damit die Spannmatrize
- die Bauteile werden nach der OP20 Bearbeitung manuell durch Bediener gereinigt und entgratet
- die Fertigteile werden im KLT-Behälter abgelegt und von der Logistik abgeholt
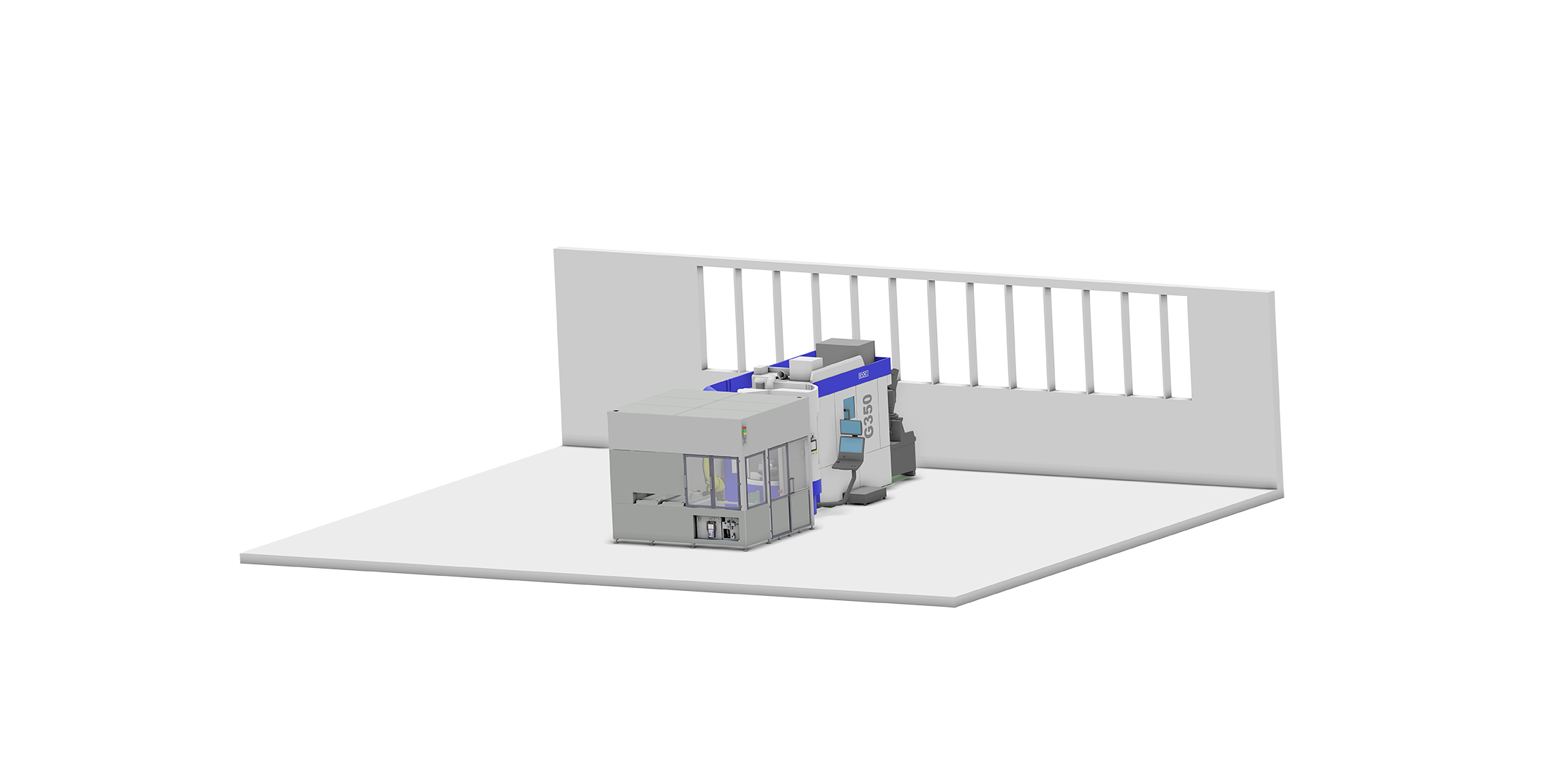
Nachher – smarte Schüttgut Be- und Entladung
- Schüttgutteile werden je nach Variante auf Ablagefläche in der Zelle entleert
- Kamera erkennt Lage der einzelnen Bauteile und übergibt Koordinaten dem Zellenroboter
- mit dem Magnetgreifer werden Gussteile aufgenommen und der Bearbeitungsmatrize zugeführt
- nach der OP10 Bearbeitung werden Bauteile zurück in den Container gelegt und automatisch ausgeschleusst
- nach dem Zwischenprozess erfolgt die automatische Entnahme, ohne Kameratechnik, aus dem Bauteilcontainer durch den Zellenroboter
- nach dem OP20 Prozess werden die Gussbauteile an einer pneumatischen Spindel entgratet, gebürstet und im Ultraschallbecken gereinigt
- final werden die Teile durch die Robotik geordnet im KLT-Behälter für den Versand abgelegt
Drehmaschine
Anbindung an die automatische Intralogistik
Leitsatz: Wir machen Sie flexibel
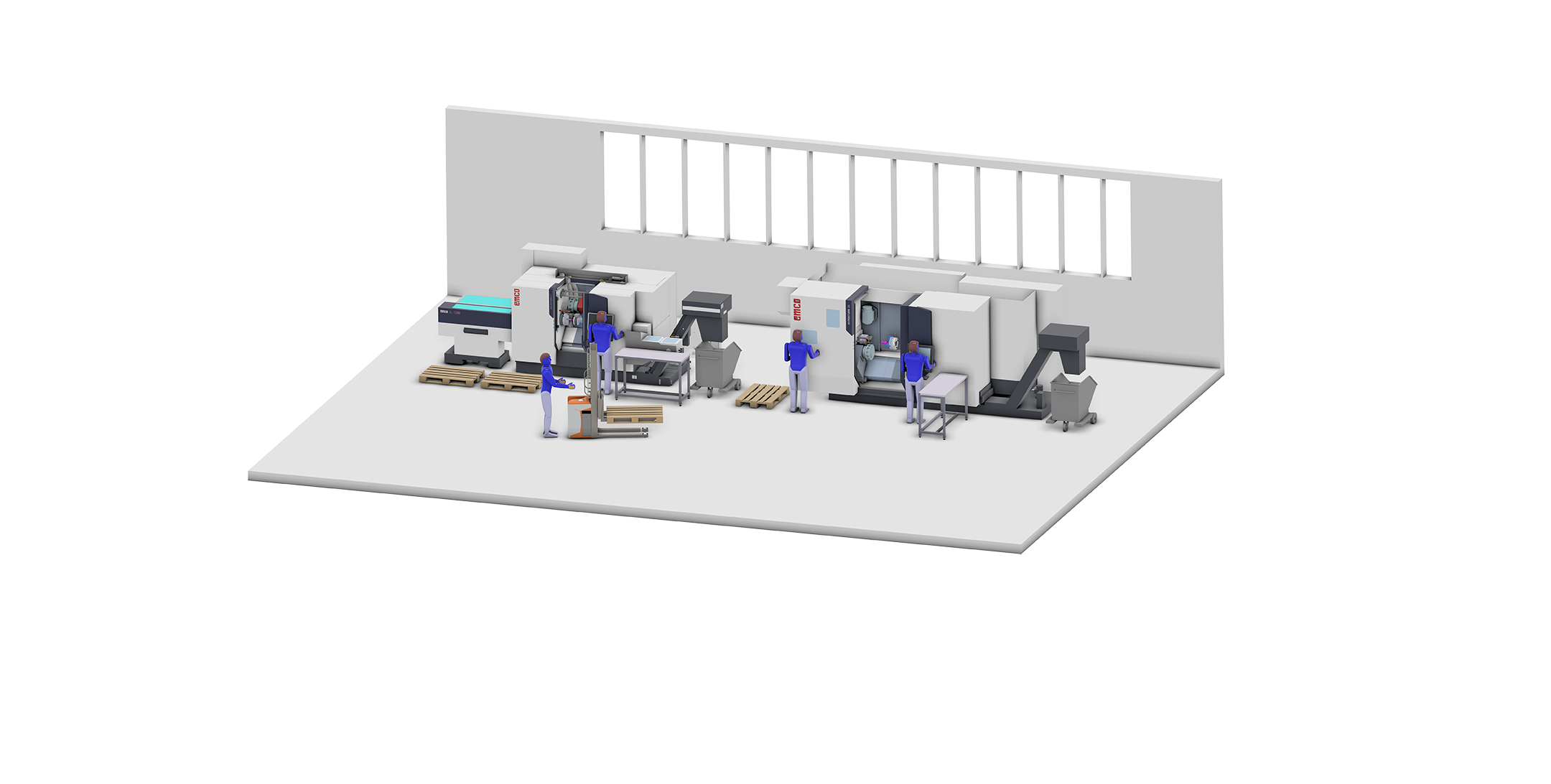
Vorher – manuelles Rüsten der Spannbacken vom Drehfutter
- Bauteile werden per Stapler in KLT-Boxen an die Anlage geliefert
- Mitarbeiter entnimmt Bauteile aus Behälter und rüstet Anlage
- je nach Bauteilvarianten müssen Spannbacken vom Drehfutter manuell angepasst werden
- manuelles Ausdrehen der Spannbacken der Gegenspindel für die OP20 Bearbeitung nötig
- ablegen der ausgedrehten Spannbacken in Maschinenschublade
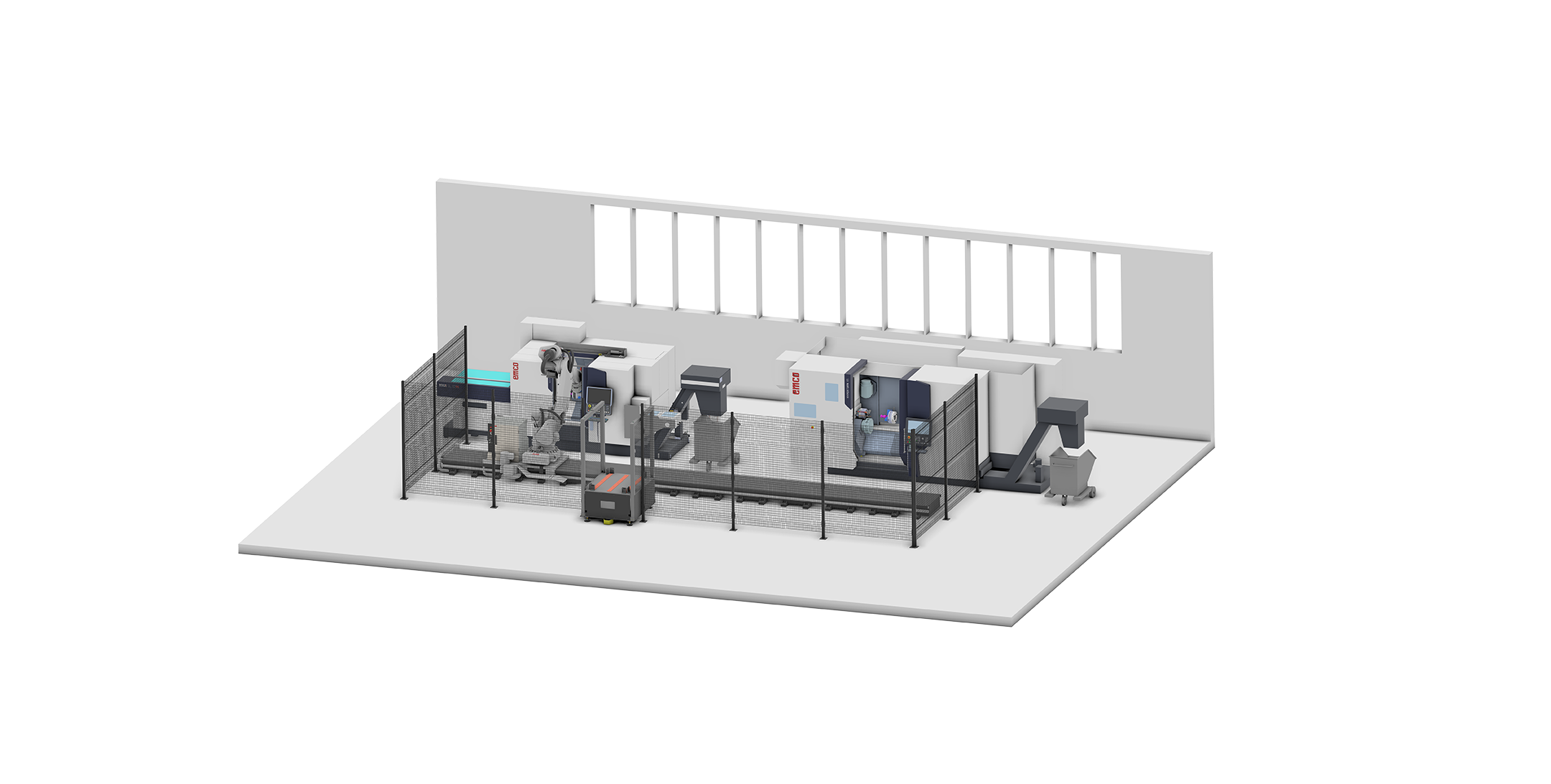
Nachher – vollautomatisierter Rüstprozess Spannbacken
- Rohteile werden per automatisierter Intralogistik(AGV) der Anlage zugeführt
- Rohteile sind im KLT-Behälter bereits roboterentnahmetauglich positioniert
- Entnahme und Bauteilrüsten erfolgt per Roboter auf 7ter Achse
- nach der Bearbeitung werden Fertigteile gewaschen und in KLT-Behälter zurückgelegt
- Intralogistik holt Fertigteile automatisch per Auftragsmanagementsoftware ab
- Spannbackenrüstprozess und Greifbackenrüstprozess erfolgt vollautomatisch
- auch Gegenspindelrüstprozess ist mit der Robotik komplett automatisiert
Fertigungsanlagen
mit Vorrichtungs- und Werkstückhandling
Leitsatz: mannlose 24/7 Fertigung
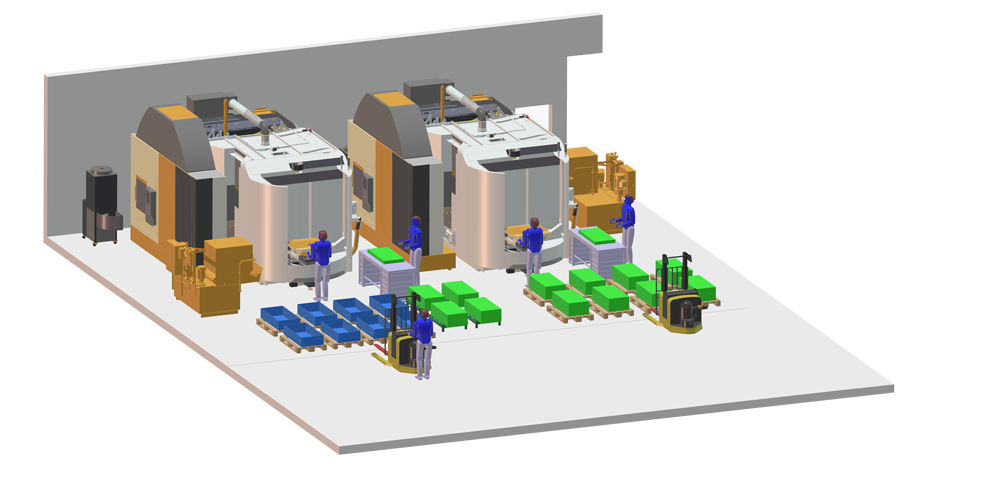
Vorher – manueller Arbeitsablauf
- Rüsten der Werkstückspannvorrichtung in den Fertigungsanlagen durch Bedienpersonal
- Be- und Entladen der Rohteile bzw. Fertigteile durch Bediener per Kran
- Bauteilendkontrolle auf Beschädigungen und Lunker durch Qualitätsprüfer
- vor den Anlagen großer Platzbedarf für Vorrichtungs-, Rohteil- und Fertigteilmanipulation
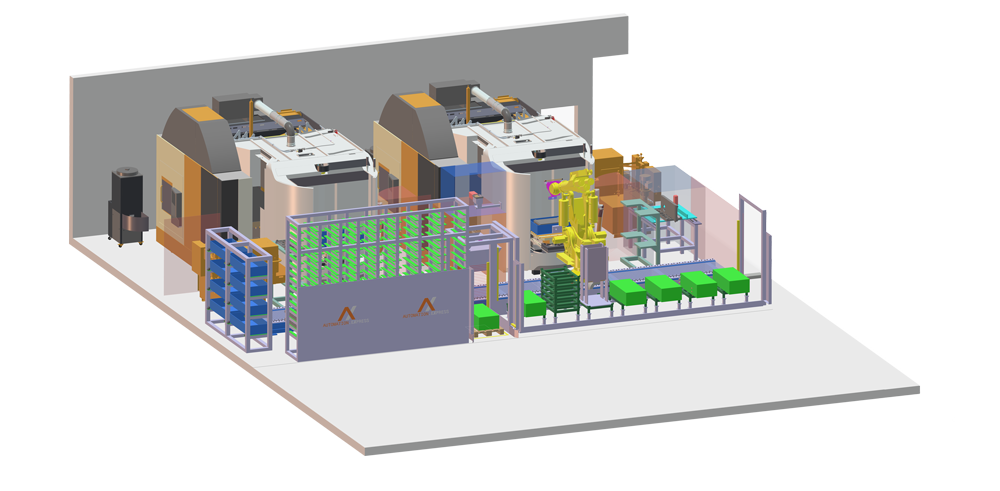
Nachher – vollautomatische Lösung
- unterschiedliche Rohteiltypen Einschleusung auf Europalette mit Bauteilerkennung über 3D-Visionsensorik zur Robotikaufnahme
- Rohteil- und Vorrichtungsmanipulation mittels 6-Achs Roboter auf 7ter Achse zwischen beiden Fertigungsanlagen
- Rohteilpufferung und Vorrichtungsbahnhof zur autarken 24/7 Produktion
- Qualitätssicherung nach Zerspanung über 3D-Oberflächeninspektion
- Robotergesteuerter Entgratprozess mit Absaugung zur Finalisierung des Fertigteiles
- Ausschleusung des geprüften Fertigteiles auf eigene Variantenlademittelträger oder Ablage auf Ausschusslademittelträger
- Robotermanipulation der Kunststoffzwischenleisten zum Schutz der Fertigteile bei Stapelung auf Lademittelträger
- Auftragssteuerung(JIS) und Protokollierung über Schnittstelle mit übergeordnetem Leitsystem
➜ Vorrichtungs- oder Rohteilgewicht bis zu 400kg
Werkzeugmaschine
mit AX-Palettenspeicher
Leitsatz: Treffen Sie bessere Entscheidung.
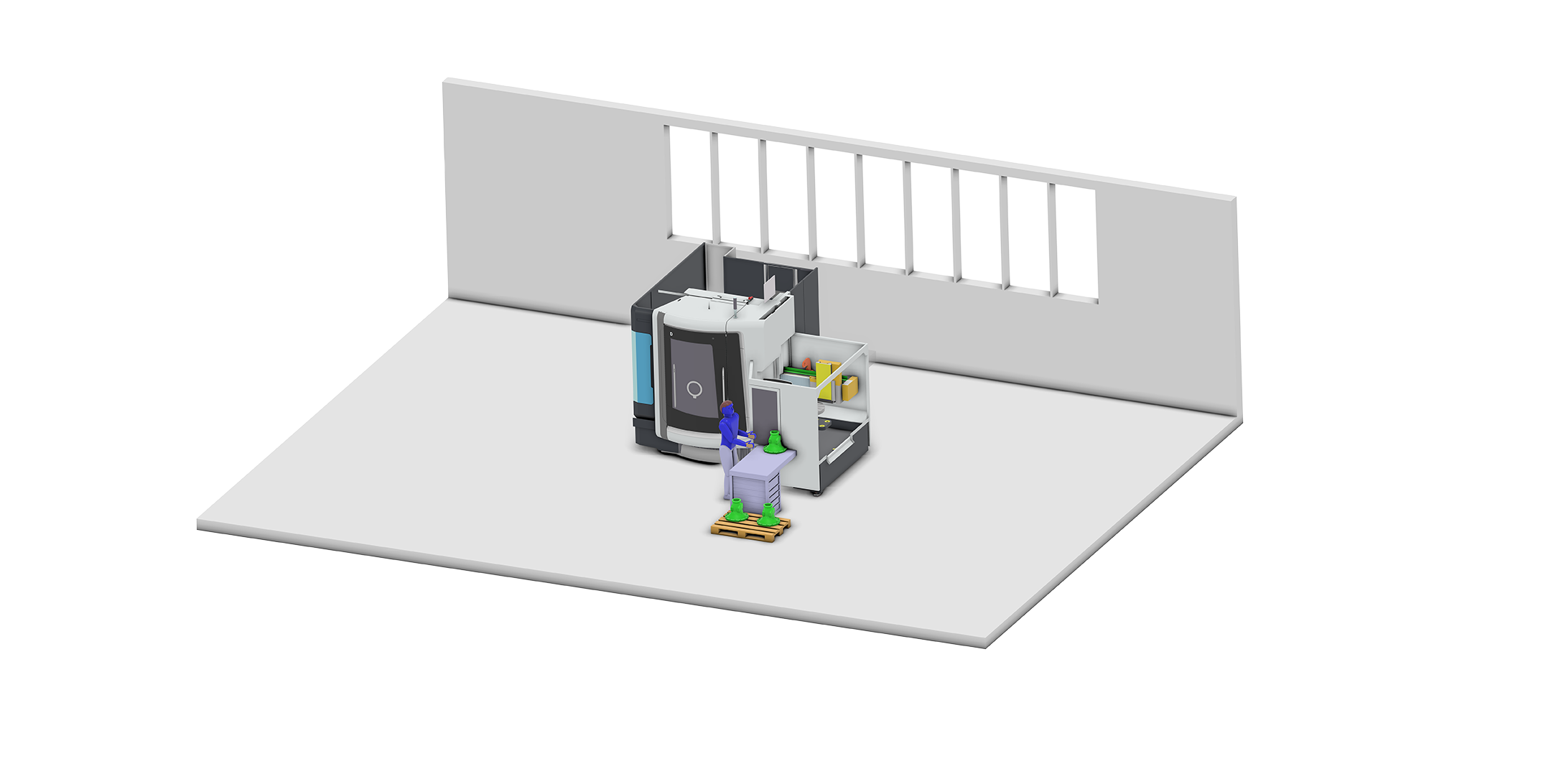
Vorher – einfacher Rüstprozess
- Bauteile werden durch Werker einzeln in Maschine gerüstet
- Werker muss immer bei Programmende zum Rüsten an der Anlage stehen, ansonsten lange Stillstandszeiten
- keine mannlose Fertigung über mehre Bauteile möglich
- bei Bauteilvariants = manueller Spannmittelwechsel
- aufwendiger Spannmittelwechsel = lange Stillstandszeit der Maschine
- während des manuellen Rüstprozess keine Zerspanung möglich
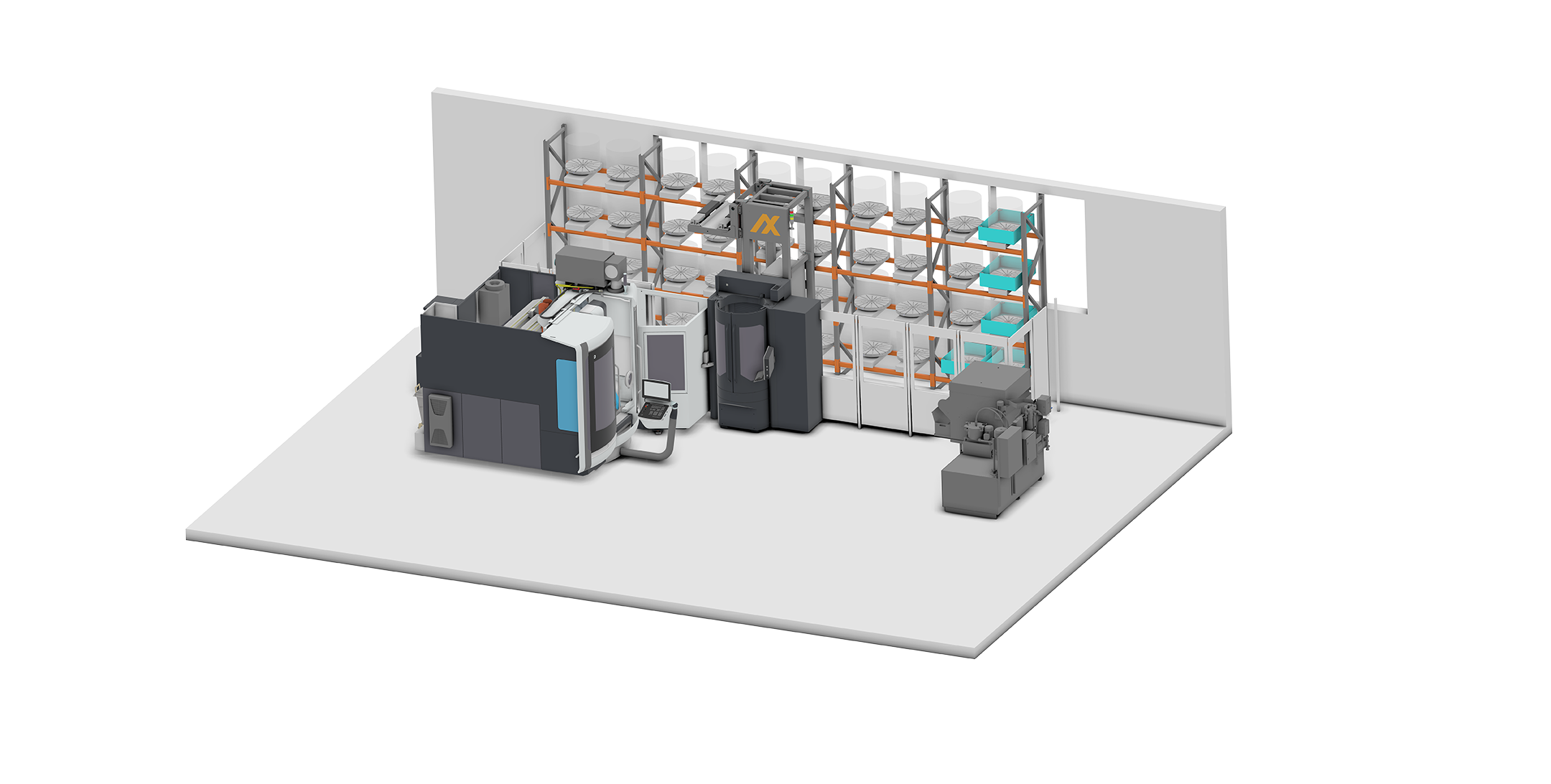
Nachher – AX-Palettenspeicher
- unabhänging vom Fertigungsprozess werden Bauteile vom Werker in der Rüststation gerüstet
- AX-Palettenhandlingsgerät entnimmt Bauteile aus Rüststation und puffert diese im Lager zwischen
- mit AX-Software Erstellung und Steuerung von gesamten Fertigungsaufträgen (mannlose Fertigung)
- mit AX-Maschinenschnittstelle Übergabe von NC-Programm, Werkzeugdaten Überprüfung, uvm.
- hochflexible Paletten System Verwaltung
- durch AX-Palettenhandlingsgerät keine Stillstandszeiten
➜ Vorrichtungs- oder Rohteilgewicht bis zu 700kg
mehrere Werkzeugmaschinen
mit AX-Palettenlager
Leitsatz: Wir machen Sie flexibel.
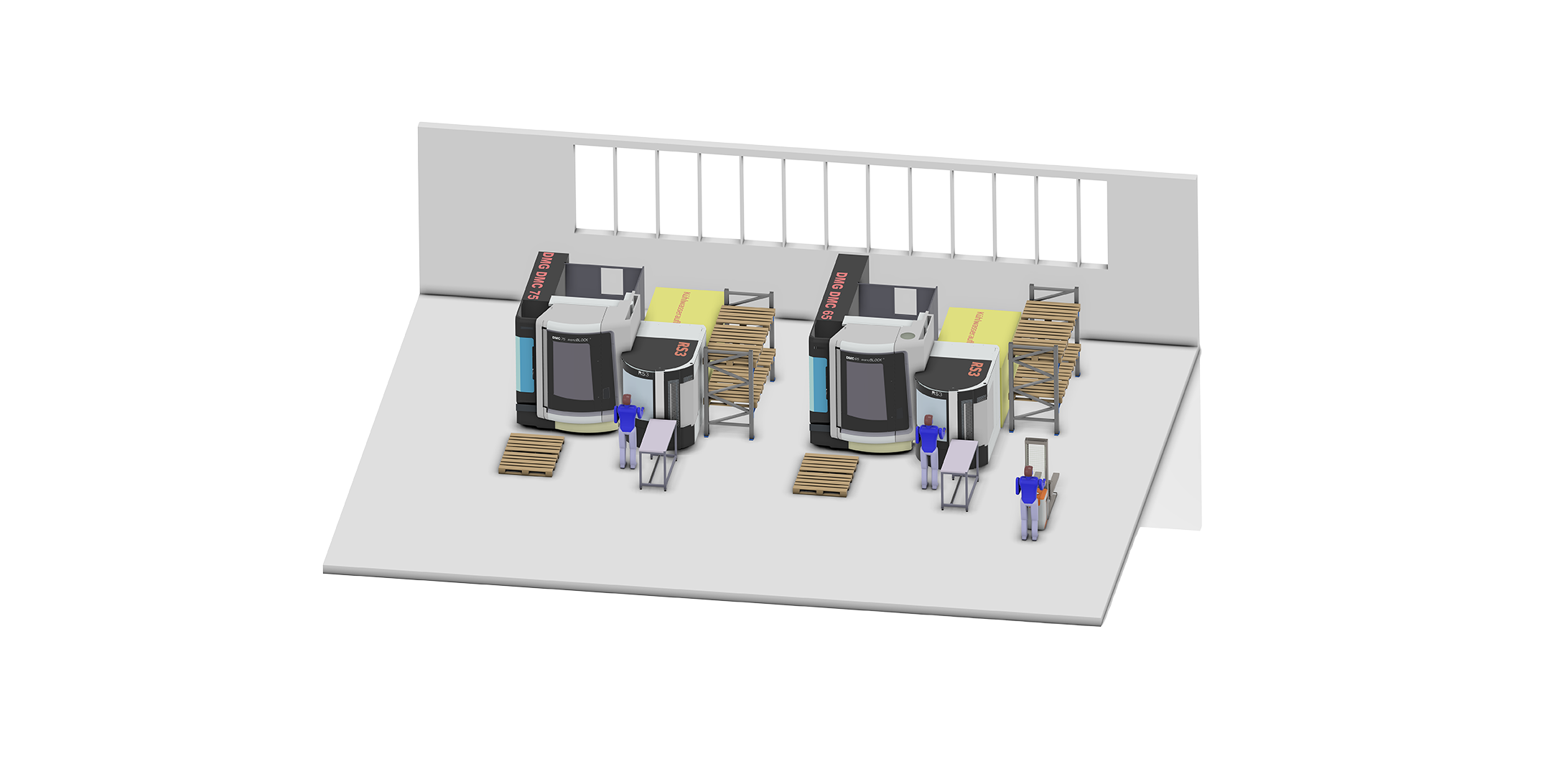
Vorher – zeitintensiver Rüstprozess
- Bauteile werden durch Werker einzeln in beide Maschinen gerüstet
- Werker muss immer bei Programmende zum Rüsten an der Anlage stehen, ansonsten lange Stillstandszeiten
- keine mannlose Fertigung über mehre Bauteile möglich
- bei Bauteilvariants = manueller Spannmittelwechsel
- aufwendiger Spannmittelwechsel = lange Stillstandszeit der Maschine
- während des manuellen Rüstprozess keine Zerspanung möglich
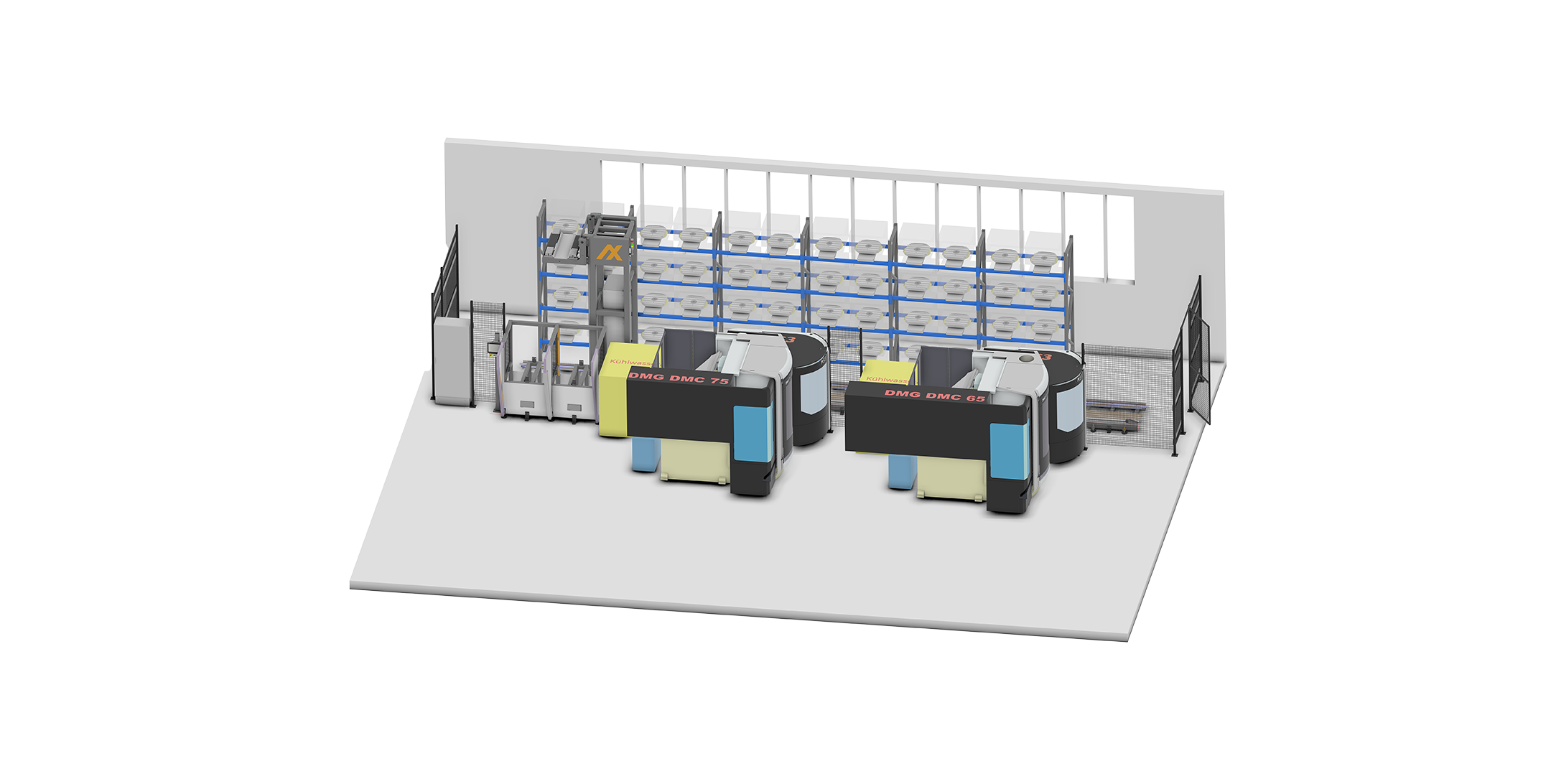
Nachher – AX-Palettenlager mit Bestandsanlagen
- unabhänging vom Fertigungsprozess werden Bauteile vom Werker in der Rüststation gerüstet
- Zwei Rüststationen geben maximale Flexibilität (z.B. 1x Rohteilrüsten, 1x Fertigteilrüsten)
- AX-Palettenhandlingsgerät entnimmt Bauteile aus Rüststation und puffert diese im Lager zwischen
- mit AX-Software Erstellung und Steuerung von gesamten Fertigungsaufträgen (mannlose Fertigung)
- mit AX-Maschinenschnittstelle Übergabe von NC-Programm, Werkzeugdaten Überprüfung, uvm.
- hochflexible Paletten System Verwaltung
- durch AX-Palettenhandlingsgerät keine Stillstandszeiten
- Palettenübergabe ins DMG RS3 Rundspeichersystem möglich
➜ Spannmittel oder Rohteile können ebenfalls im Regal gelagert werden
Produktionsmaschinen
Produktionsanlagen
mit rotierender Gitterbox Logistik
Leitsatz: monotone Arbeiten automatisieren
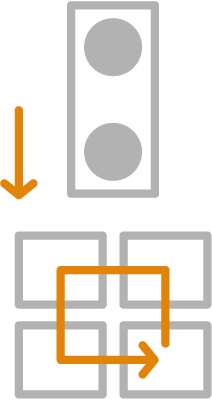
Gibo-Logistik
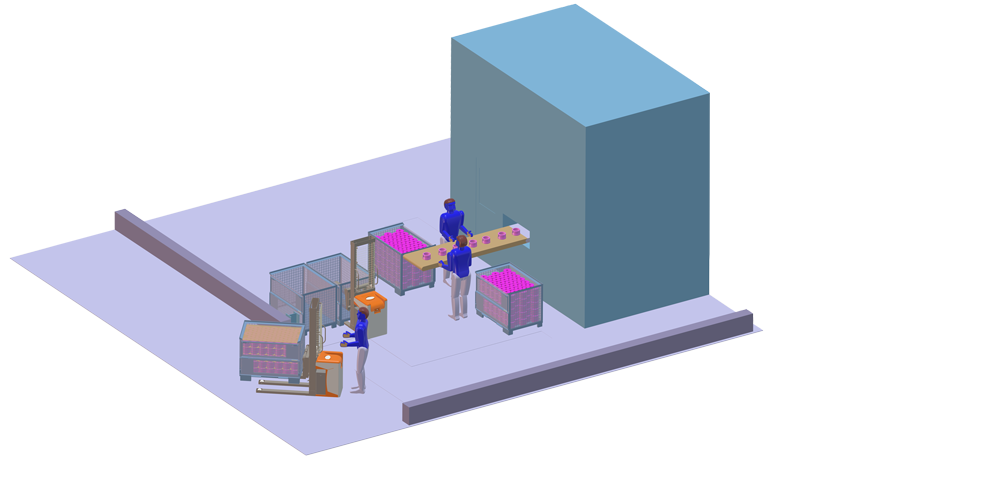
Vorher – manuelle Gitterboxen Bestückung vom Förderband einzeln
- Bauteile werden von Hand vom Förderband entnommen
- Ablage der Bauteile in der Gitterbox nach definiertem Lagenbild
- Taktzeit 1,4sec pro Bauteil – mehrere Bauteilvarianten
- Gitterboxen werden per elektrischem Hubwagen vor Anlage positioniert
- Gitterboxenaustausch (voll/leer) erfolgt durch zusätzlichen Bediener
- Kartonzwischenlagen werden bei Bedarf in Gitterbox eingelegt
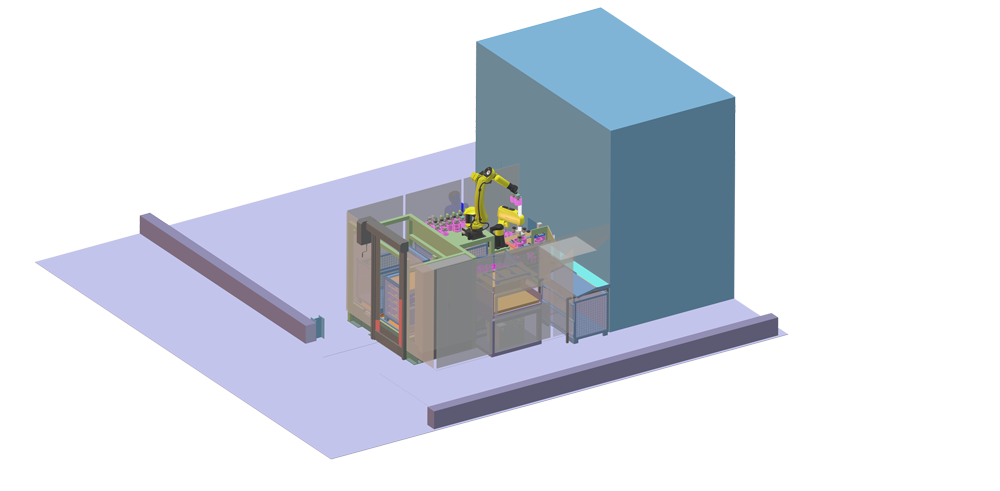
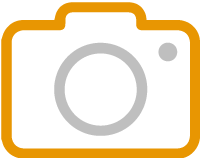
Nachher – Gitterboxen Beladung
- Bauteile werden am Förderbandende zur Roboterentnahme zentriert
- 4-Achs Scara Roboter entnimmt Bauteile und stapelt diese zu Türmen = Bauteilpufferung
- Türme werden dann vom 6-Achsroboter aufgenommen und in Gitterbox abgelegt
- volle Gitterbox wird mittels Anlagentransporttechnik zur GiBo-Entnahmeposition getaktet
- leere Gitterbox wird automatisch zur Roboter Beladeposition bewegt
- Kartonzwischenlagen werden per Vakuummanipulator nach jeder Bauteillage eingelegt
- bei Bauteilwechsel erfolgt automatischer Werkzeugwechsel an Robotik und Geländereinstellung am Förderband
➜ Anstatt Gitterbox können auch andere Ladehilfsmittel (Paletten, Boxen, Container, Blister,…) verwendet werden
Produktionsanlagen
mit wechselseitiger Gitterbox Logistik
Leitsatz: Fachkräfte für höherwertige Arbeitsprozesse einsetzen
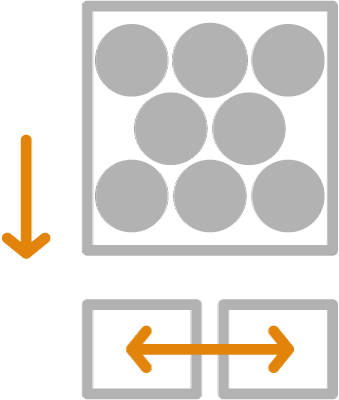
Gibo-Logistik
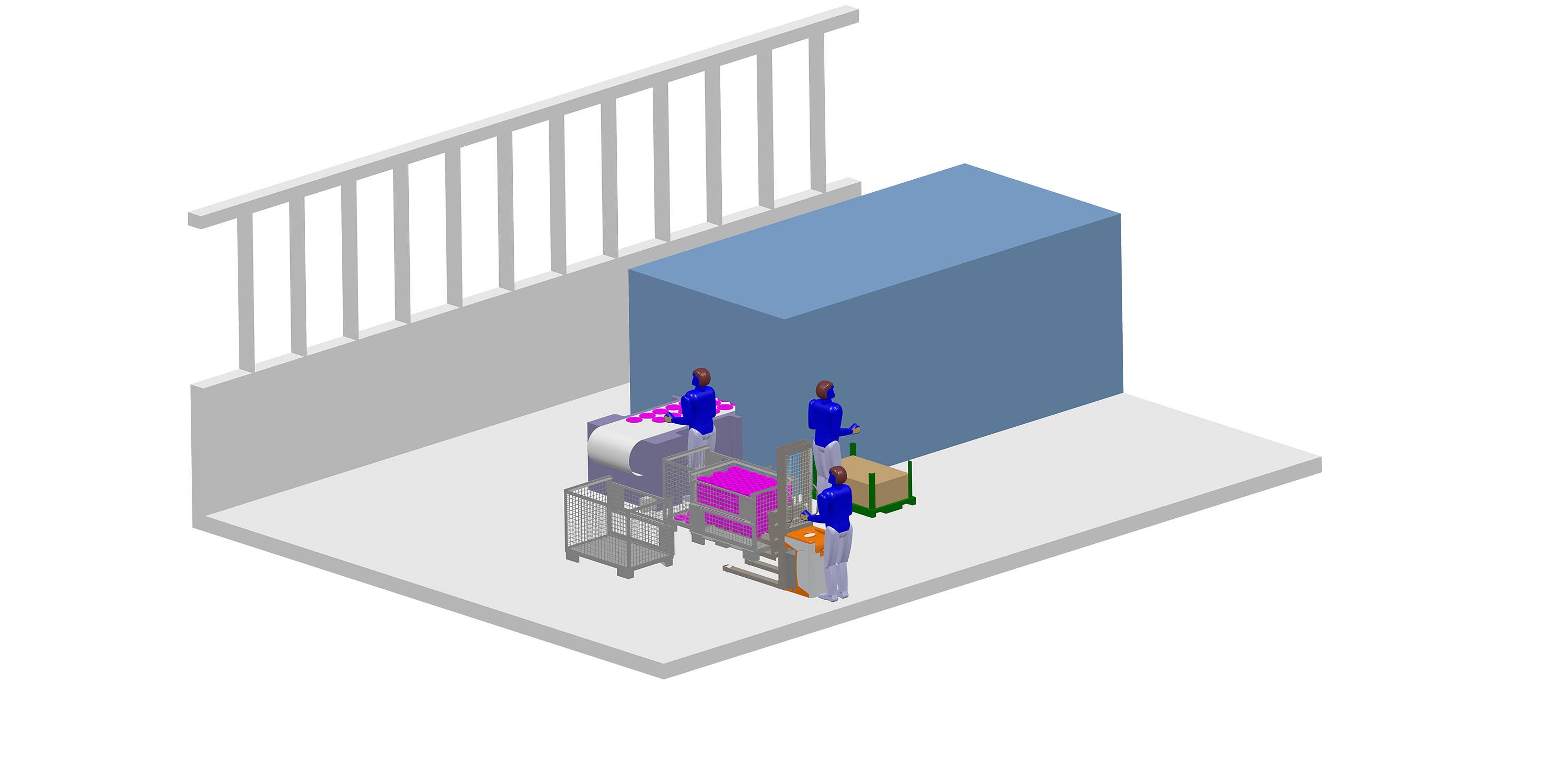
Vorher – manuelle Gitterboxen Bestückung
- Bauteile werden von Hand vom Förderband entnommen
- Ablage der Bauteile in der Gitterbox nach definiertem Lagenbild
- Förderbandgeschwindigkeit 250mm/min - mehrere Bauteilvarianten
- Gitterboxen werden per elektrischem Hubwagen vor dem Förderband positioniert
- Gitterboxaustauch (voll/leer) erfolgt durch zusätzlichen Bediener
- Kartonzwischenlagen werden bei Bedarf in Gitterbox eingelegt
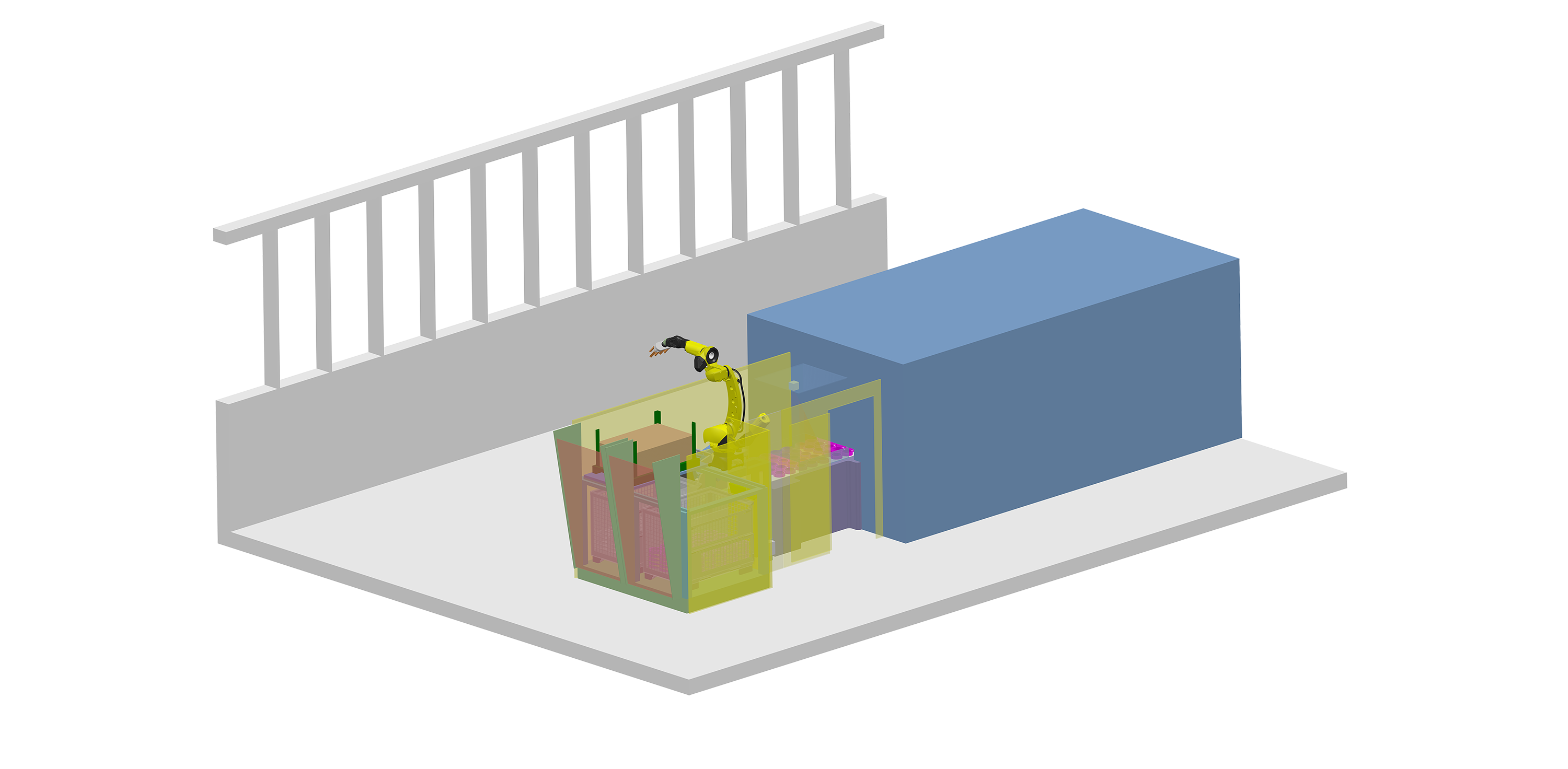
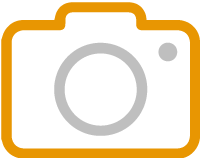
Nachher – Gitterbox Beladung vom Förderband mehrfach
- mehrere Bauteile nebeneinander werden gleichzeitig auf Förderband aus Produktionsanlage gefördert
- Bauteilpositionen werden durch Vision Kamera erfasst und Koordinaten an die Robotik übergeben
- Roboter greift Bauteile dynamisch vom fortlaufenden Förderband und stapelt diese in Gitterbox
- Zwischenlagen werden nach jeder vollen Bauteillage per Roboter gesetzt
- wenn Gitterbox befüllt, wechselt Roboter zu leeren Gitterbox, und volle GiBo wird entnommen
- bei Bauteilwechsel erfolgt automatischer Werkzeugwechsel am Greifer
➜ Anstatt Gitterbox können auch andere Ladehilfsmittel (Paletten, Boxen, Container, Blister,….) verwendet werden
Produktionsanlagen
mit linearer Gitterbox Logistik
Leitsatz: vollautomatischer Produktionsprozess
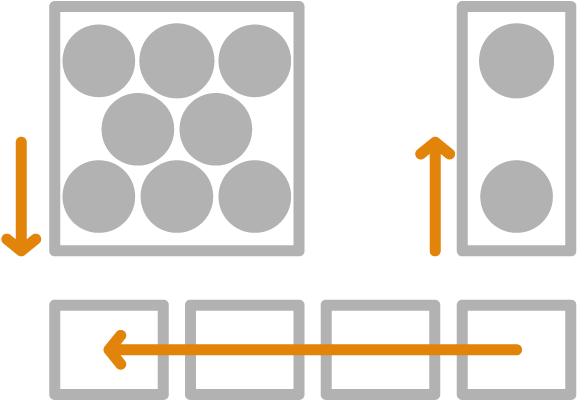
Gibo-Logistik

Vorher – manuelle Bauteil Be- und Entladung
- Bauteile werden von Hand aus Gitterbox entnommen und am Anlagenzuführförderband abgelegt
- Kartonzwischenlagen aus der Entnahme werden gesammelt
- Bauteile werden durch Produktionsanlage geschleust
- am Ende des Produktionsprozessen werden Bauteil am Förderband aus Anlage gefördert
- Mitarbeiter entnimmt Bauteile vom Förderband und stapelt Bauteile in Gitterbox
- Zwischenlage werden von der Sammelposition entnommen und bei der Gitterbox Befüllung wiederverwendet
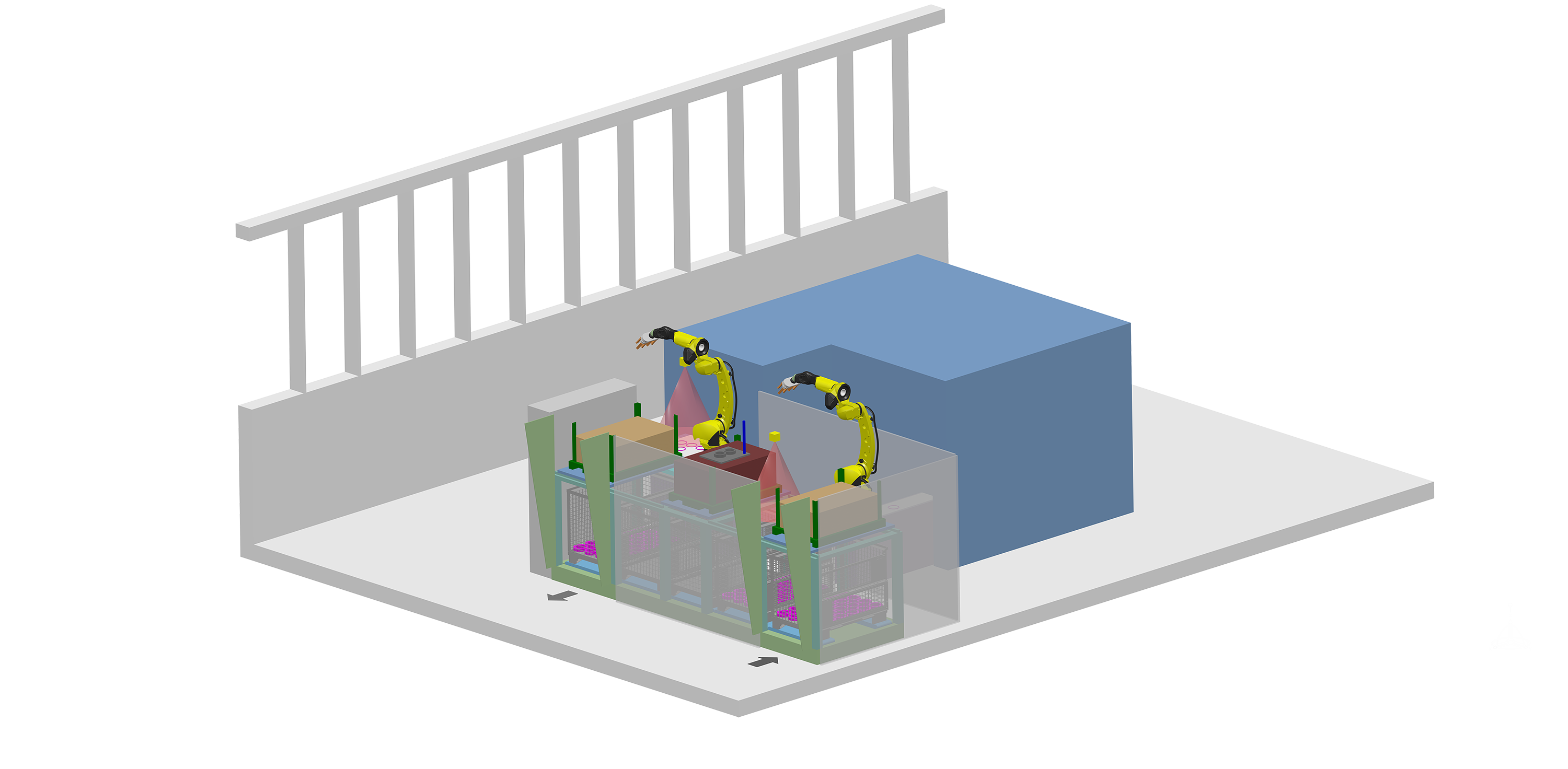
Nachher – automatische Be- und Entladung
- Bauteilpostionien in Gitterbox werden von Vision Kamera detektiert und an Robotik übergeben
- Roboter greift Bauteile aus Gitterbox und legt diese am Zuführförderband ab, Zwischenlagen werden zwischengepuffert
- Bauteile werden durch Produktionsanlage geschleust
- am Ende des Produktionsprozesses werden Bauteilpositionen von Vision Kamera am Förderband detektiert
- Roboter entnimmt Bauteile und legt diese in Gitterbox ab
- Zwischenlagen werden aus Puffer entnommen
- Gitterboxlogistik vom Entleeren zum Befüllen erfolgt in der Anlage
➜ Anstatt Gitterbox können auch andere Ladehilfsmittel (Paletten, Boxen, Container, Blister,….) verwendet werden
Produktionsanlagen
mit 3-Achs-Bauteilportal
Leitsatz: Effizienter. Produktiver. Sicherer.
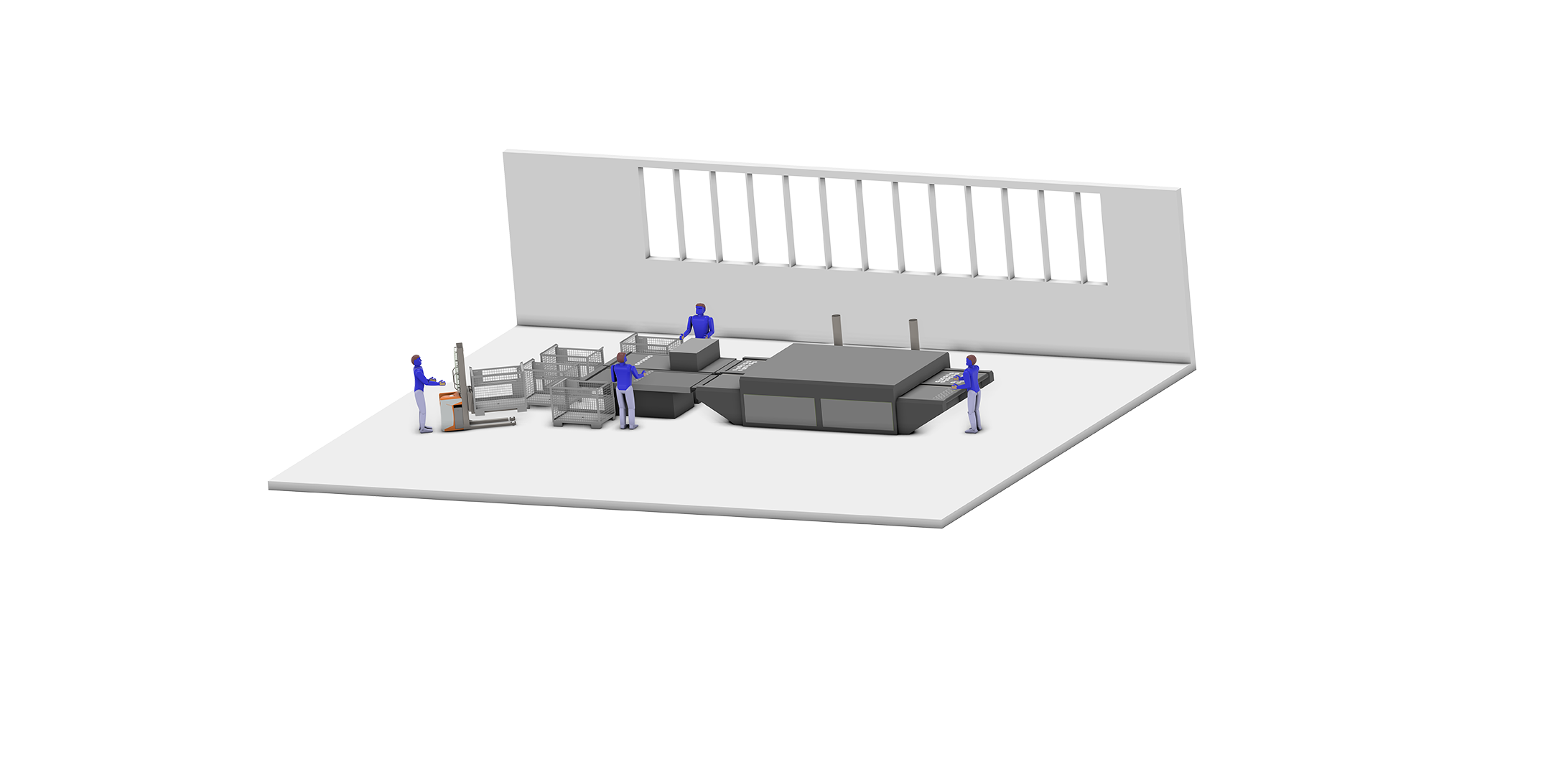
Vorher – manuelles Bestücken der Produktionsanlage
- Bauteile werden händisch vom Mitarbeiter auf Produktionsband z.B. Druckmaschine aufgelegt
- Leere Palette wird vom Mitarbeiter per Ameise umgestellt und neue an Entnahmeplatz positioniert
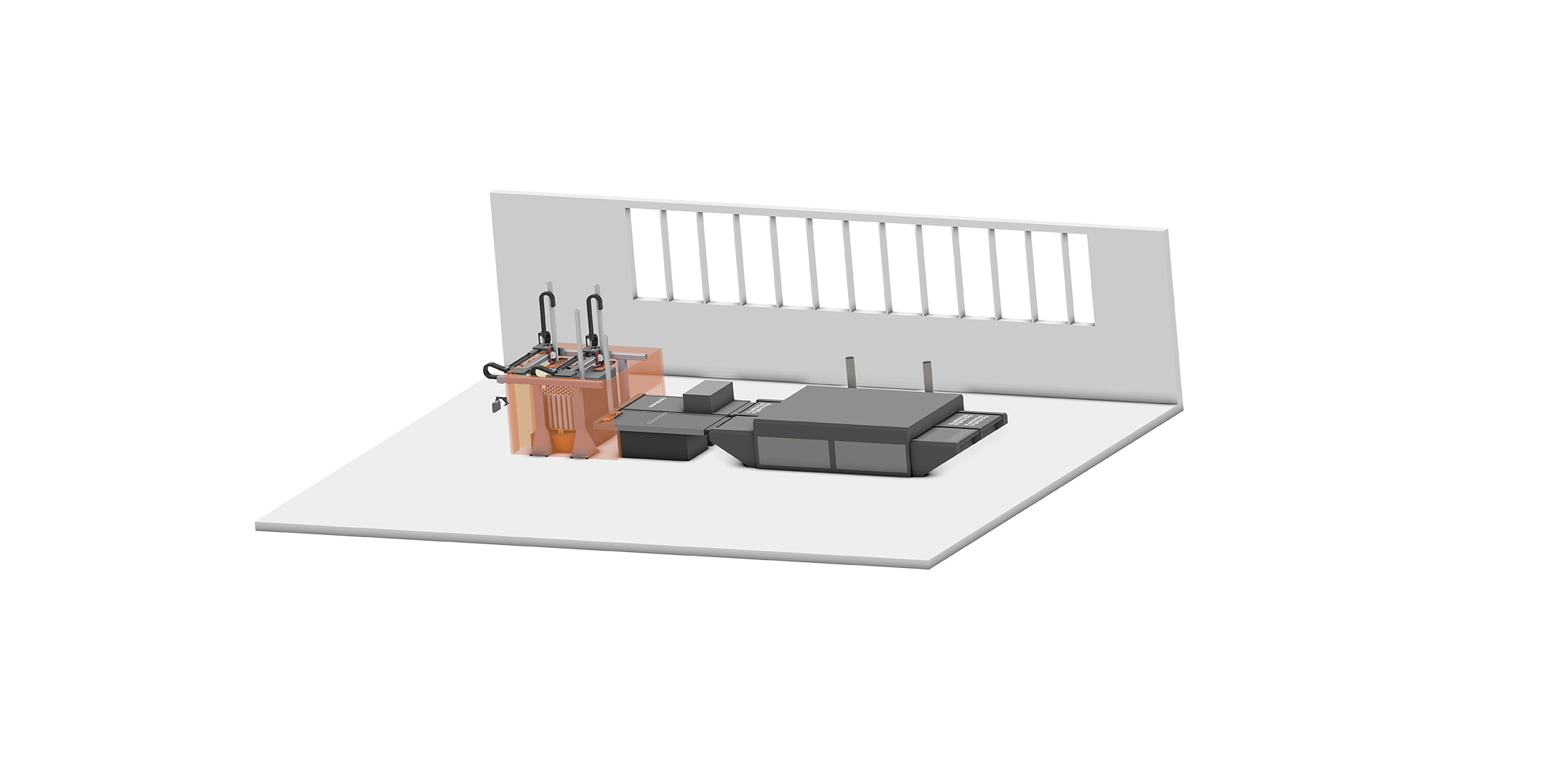
Nachher – vollautomatisierte Beladung
- im Paletten Zwei-Kammernsystem können wechselseitig die Paletten per Hubgerät Be- und Entladen werden
- 3-Achs Hochleistungsportal nimmt per Vakuumsauger Bauteile von Palette auf und legt dieses am Förderband der Produktionsanlage ab
- Durch 2 Kamerasysteme kann während der Beladung die leere Palette entnommen werden -> somit kontinuierlicher Beladeprozess
Fertigungslinien
Fertigungslinie vollautomatisch
mit Robotern und End of Line Check
Leitsatz: maximale Produktionsautonomie
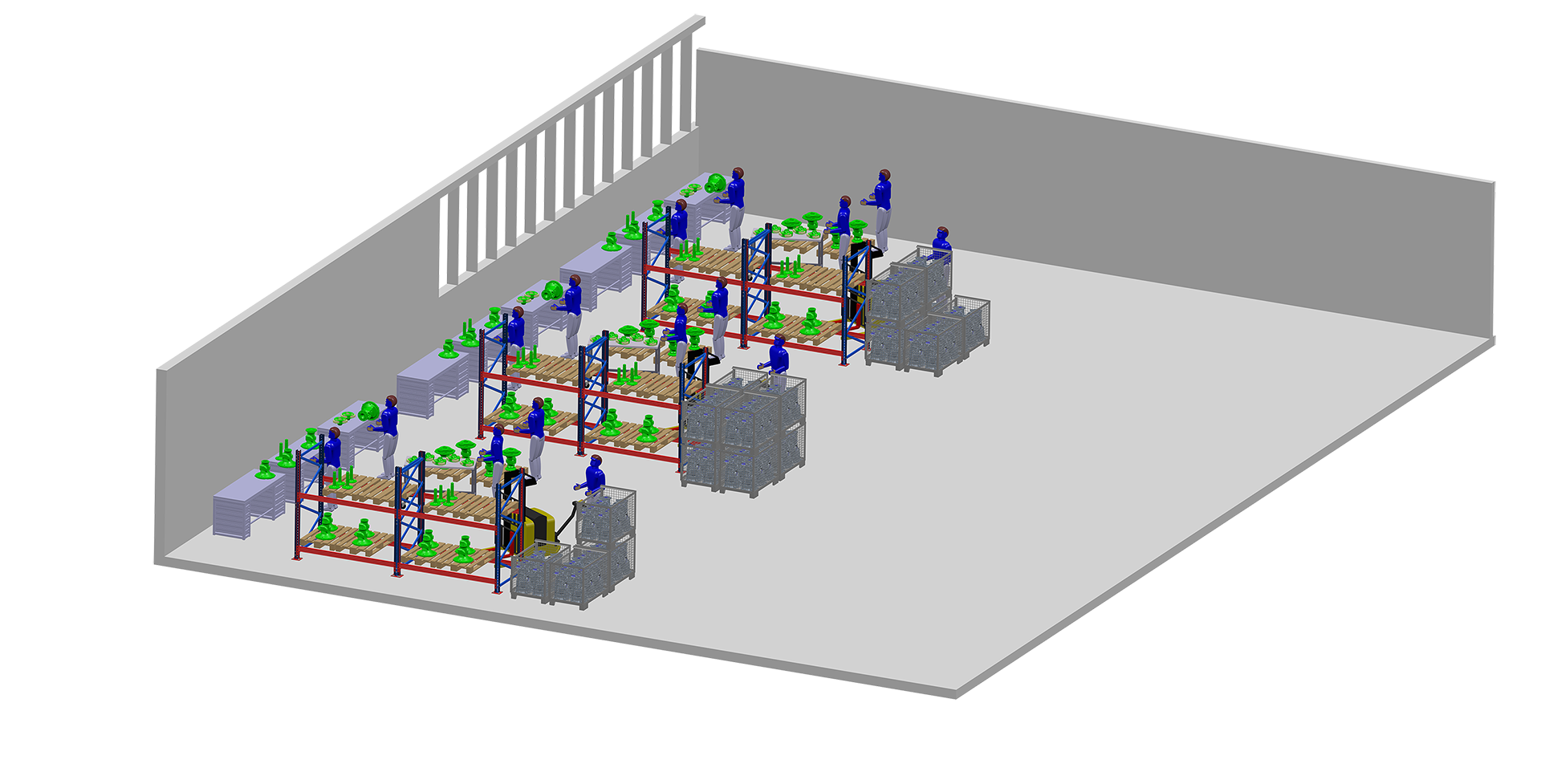
Vorher – manuelle Bearbeitungs- und Prüfprozesse
- hoher Platzbedarf für Gibo Handling und Logistik
- beeinträchtigte Stückzahlfertigung durch Störungen
- viele monotone Handlings- und Prüfarbeiten
- hohe Ausschussrate durch unkontrollierten Prozessablauf
- schlechte Ergonomie durch Bauteilhandling
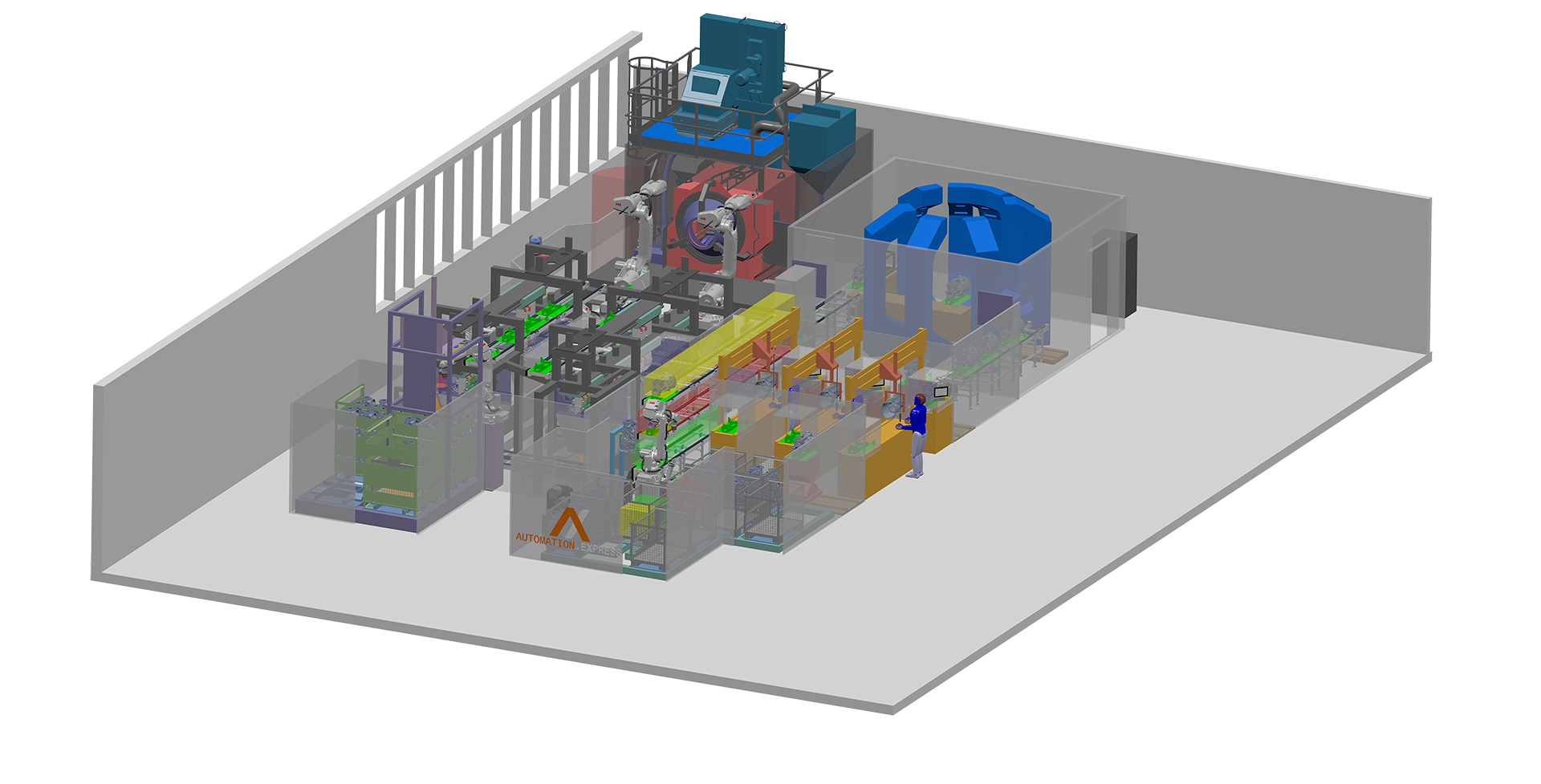
Nachher – Bearbeitungslinie mit automatisierter Oberflächen- und Geometrieprüfung
- platzsparende Ladeträgerlogistik zur Bauteileinbringung
- Robotergesteuerter Bearbeitungsprozess mit Werkzeugwechsel
- Übergabe in Sandstrahlanlage zur Oberflächenbehandlung
- autonome Oberflächen- und Teilegeometrieprüfung
- End of Line Check bei fehlerhaften Bauteilen bzw. B-Ware
- Belabelung und Bauteilverladung in Gitterboxen
Prozesslinie vollautomatisch
mit Sonderpaletten und Intralogistik
Leitsatz: Lights-out-Produktion
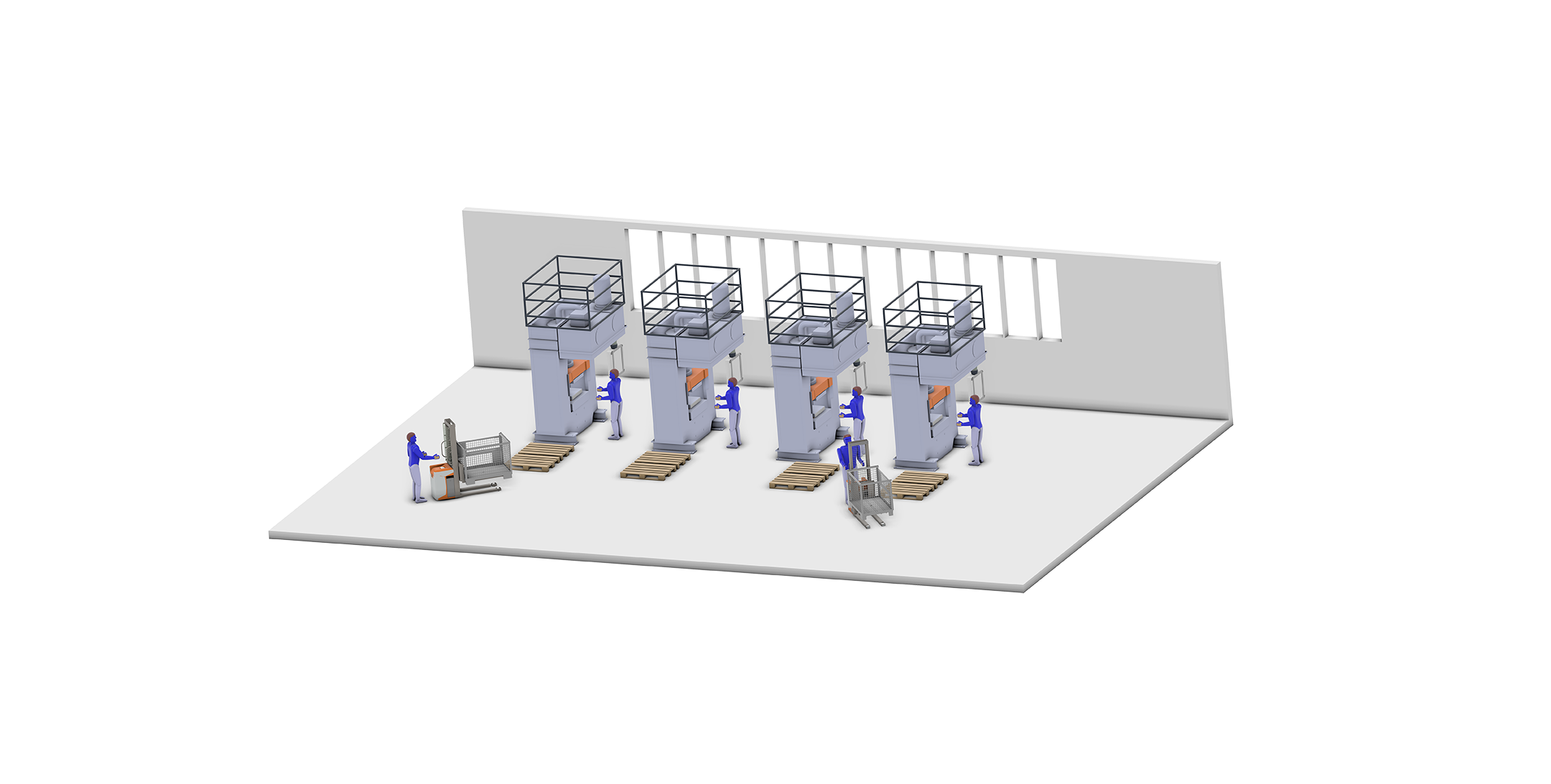
Vorher – manuelles Beladen von Pressen
- Rohlinge werden auf Wägen vor der Presse geparkt
- wenn die Presse öffnet entnimmt der Mitarbeiter den fertigen Pressling und stellt diesen auf der Seite ab
- danach kann Rohling in die Presse vom Wagen geschoben werden und Pressvorgang startet
- die Pressenparameter je nach Bauteiltyp müssen händisch vom Bediener an der Presse ausgewählt werden
- beim Auswechseln des fertigen Presslings mit dem Rohling ist immer die Anwesenheit eines Bedieners nötig
- für den Mitarbeiter unergonomisches manipulieren schwerer Rohlinge
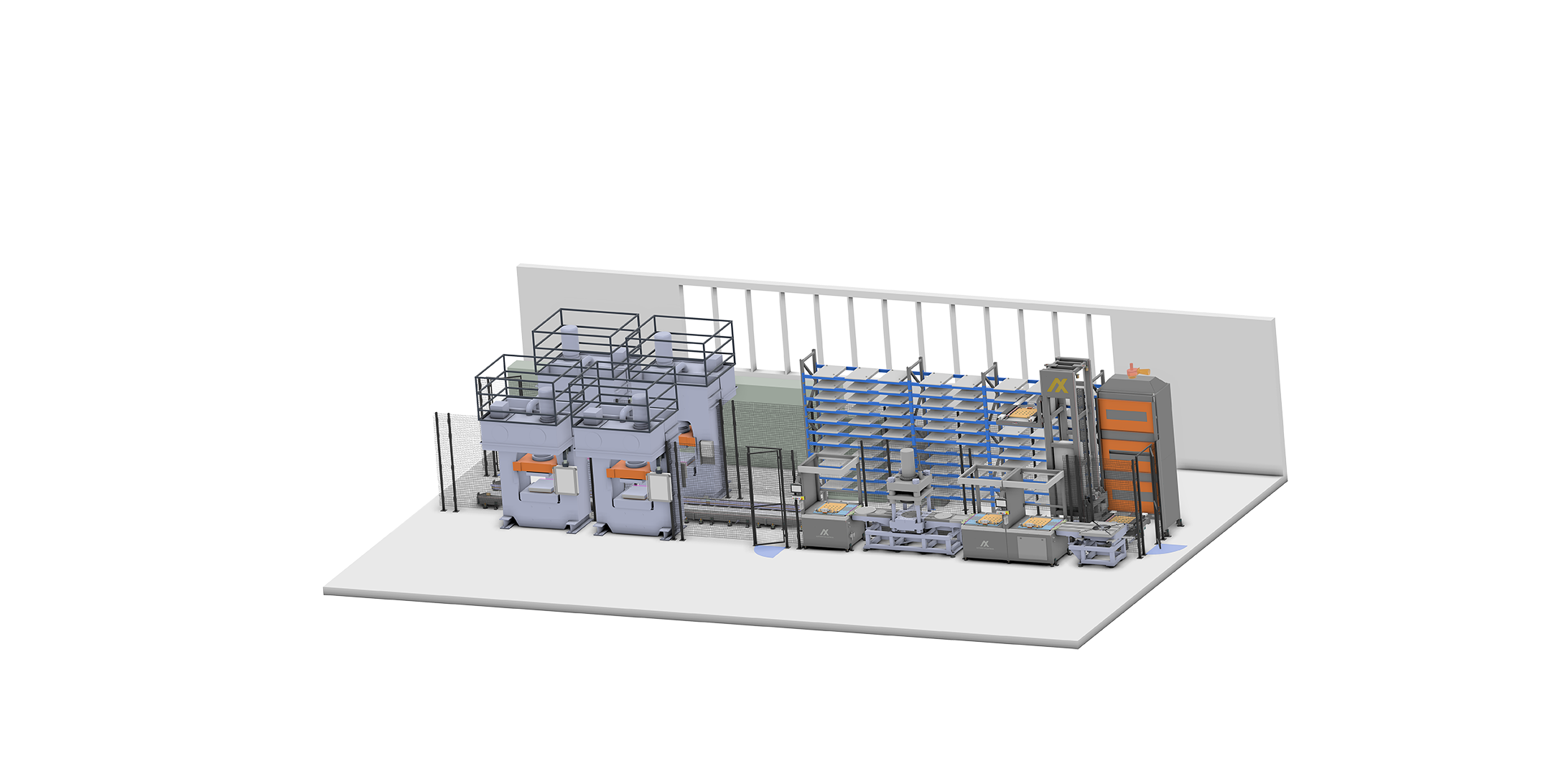
Nachher – effiziente vollautomatische Pressenbeladung
- Rohlinge werden auf Sonderpaletten im Palettenlager eingelagert
- beim Pressenöffnungstakt wartet der AX-Palettenmanipulator bereits mit dem Rohteil vor der Presse
- der Manipulator entnimmt vollautomatisch den fertigen Pressling und übergibt Rohling in die Presse zurück
- Pressenparameter können je Bauteil automatisch der Presse übergeben werden
- aufgrund der Automatisierung entstehen keine Pressenstillstandszeiten, da der AX-Palettenmanipulator immer vor der Presse auf das Öffnen wartet
- Rohlinge mit bis zu 300kg können in die Presses manipuliert werden
Prozesslinie vollautomatisch
Nachbearbeitung
Leitsatz: AX-Container als flexibler Lademittelträger
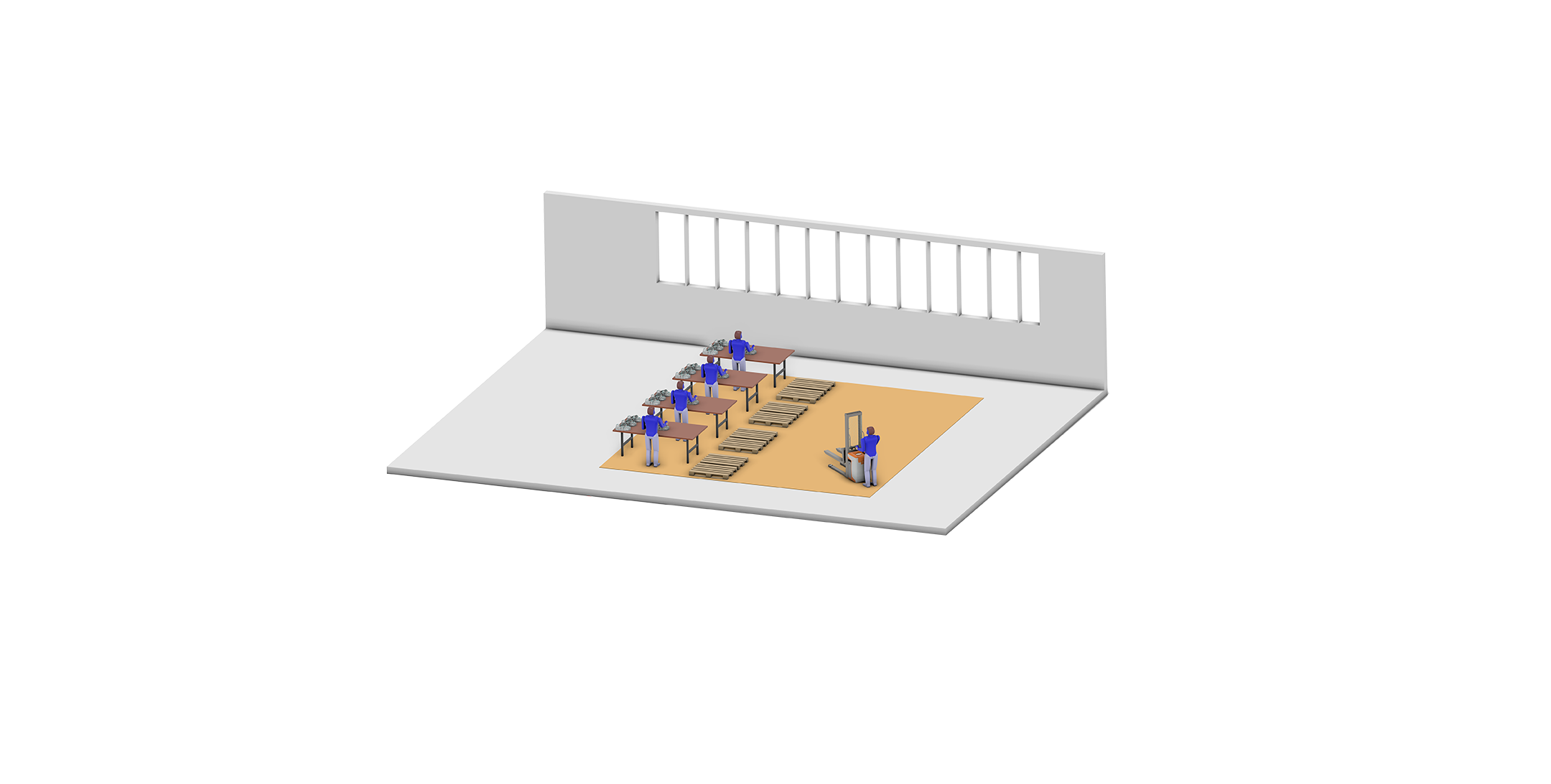
Vorher – manuelle Nacharbeit
- nach der CNC-Bearbeitung werden Bauteile auf Paletten gestapelt
- Palette mit Bauteilen werden im Nacharbeitsbereich abgestellt
- schwer zugängliche Bereiche werden vom Bediener entgratet
- Oberflächen manuell nachgebebürstet
- Bohrungen durch den Mitarbeiter gesenkt
- Ölbohrungen abgesteckt und von Spänen befreit
- final nachgearbeitete Bauteile werden auf Palette gelegt und gelangen in den Waschprozess
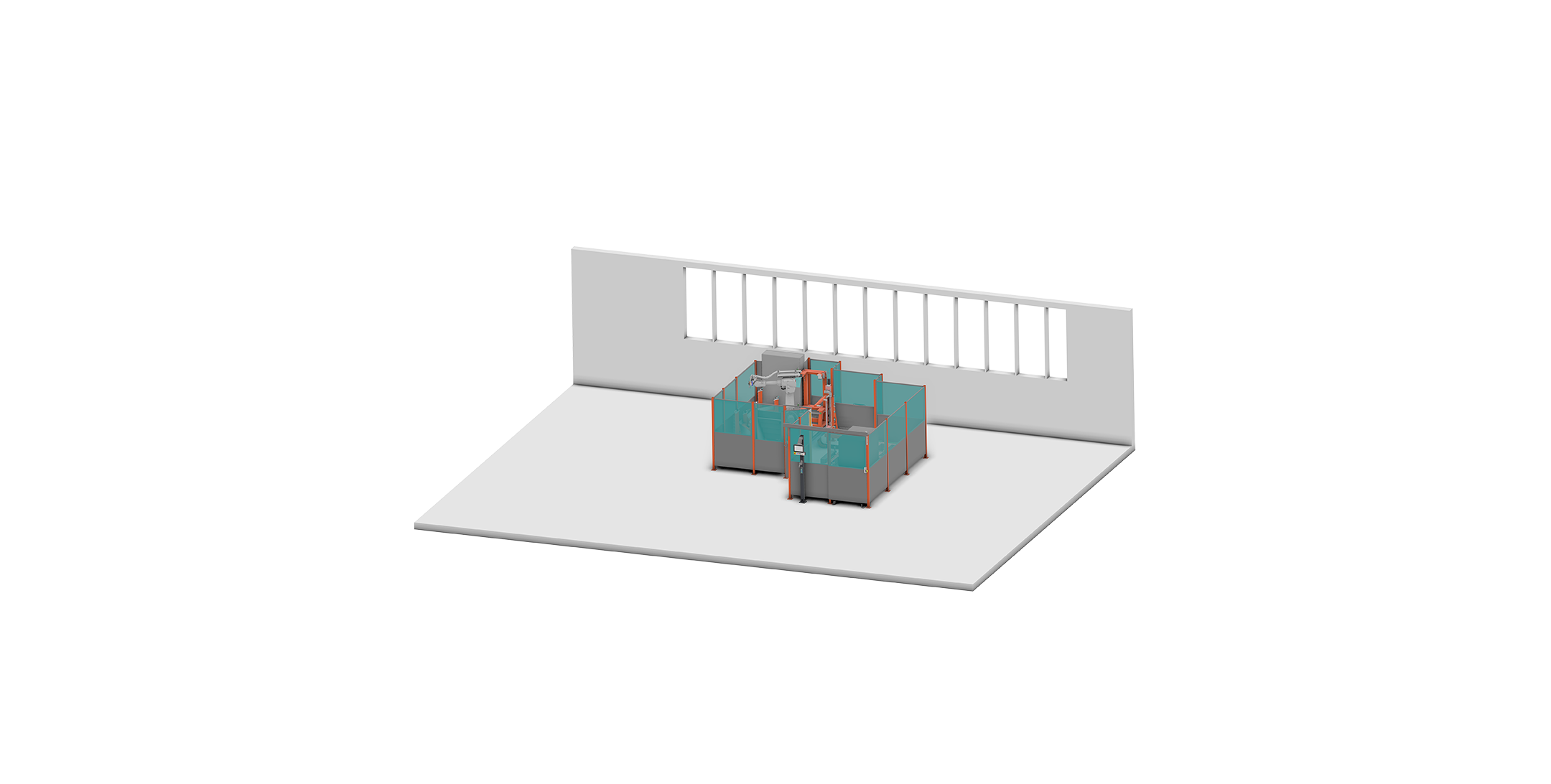
Nachher – automatisierte Nacharbeit
- nach der CNC-Bearbeitung werden Bauteile im AX-Container abgelegt
- AX-Container werden per Hubwagen in die Prozesslinie Nachbearbeitung abgestellt
- Bauteile werden vom Roboter aus AX-Container entnommen und gescannt
- Roboter manipuliert Bauteile über mehrere Spindeln mit verschiedenen Werkzeugaufsätzen entgraten, senken, bürsten und abstecken der Ölbohrungen
- Nachbearbeitetes Bauteil wird in den AX-Container abgelegt und dem Waschprozess zugeführt
Montagelinie semiautomatisch
mit kollaborierenden Robotern
Leitsatz: kontinuierlicher Montageprozess
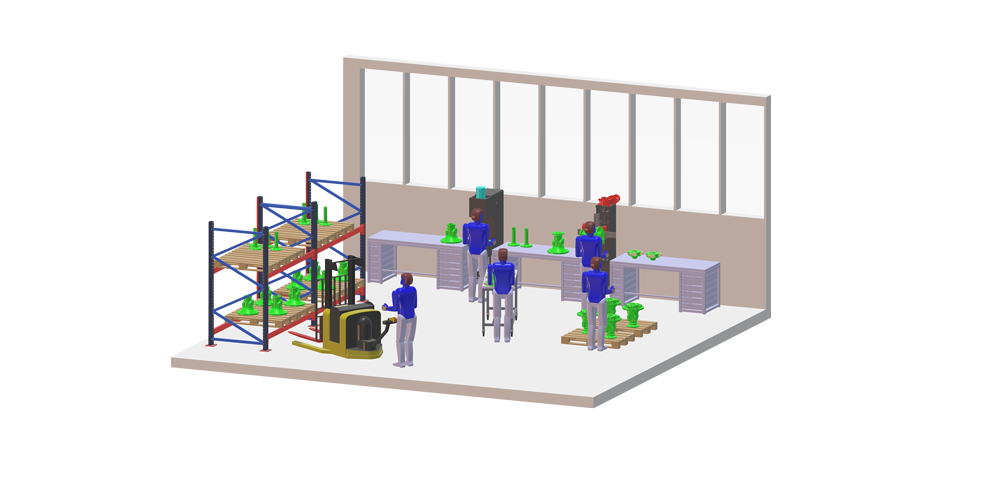
Vorher – manueller Montageprozess
- Bauteile werden zwischen den Montagestationen in Regalen gepuffert
- Montageprozess nicht ergonomisch für Mitarbeiter
- keine Dokumentation der wichtigen Prozessparameter
- unkoordinierter und unübersichtlicher Montagefluss für Mitarbeiter
- ungleichmäßige Taktzeiten in den Montagestationen
- lange Handlingszeiten von Station zu Station
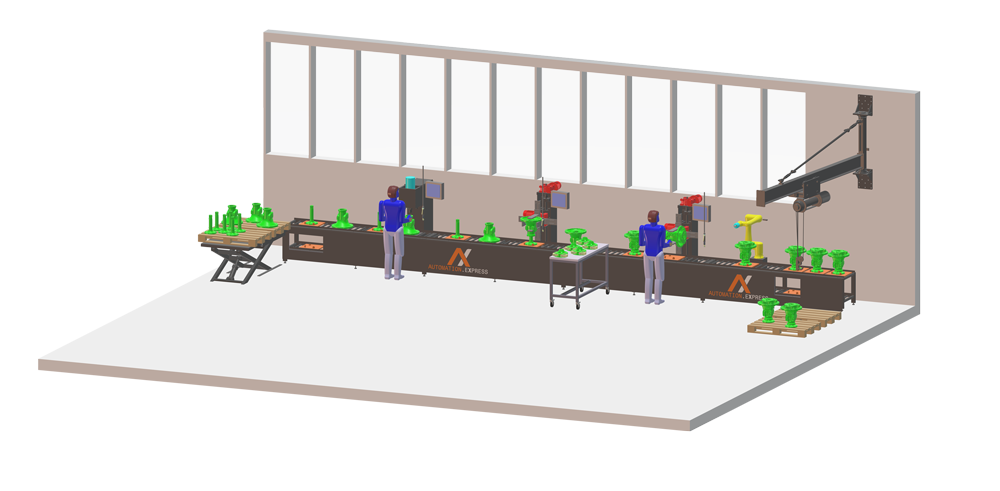
Nachher – semiautomatischer Montageprozess
- am Bandanfang wird Basisbauteil in den Montagefluss eingetaktet
- über Bauteilwägen werden diese durch die einzelnen Stationen befördert
- Montageparameter werden in den einzelnen Stationen auf Korrektheit geprüft
- Montageablauf wird über Bildschirme in jeder Station dem Personal angezeigt
- zusätzliche Montagestation ermöglicht nun gleichmäßigen Takt in jeder Station
- am Bandende werden Bauteile überprüft, dokumentiert und dem Warenausgang übergeben
- leere Wägen am Bandende werden automatisch in der unteren Montageebene wieder zurück zum Bandanfang befördert
Montagelinie vollautomatisch
mit Robotern und End of Line Check
Leitsatz: Produktivität der Fläche
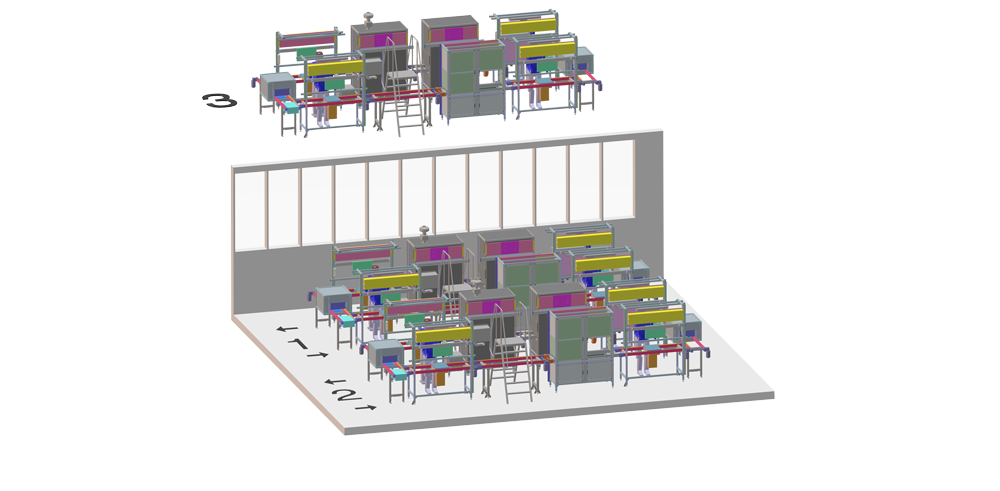
Vorher – einzelne Montagelinien
- je Montageline eigenen Be- und Entladebereiche
- lange unübersichtliche Logistikwege zur Befüllung der Schüttgutcontainer
- hohe Ausschussrate durch fehlender finaler Platinenprüfung
- längere Taktzeiten durch manuelle Montagetätigkeiten
- hoher Platzbedarf bei zusätzlicher Linie
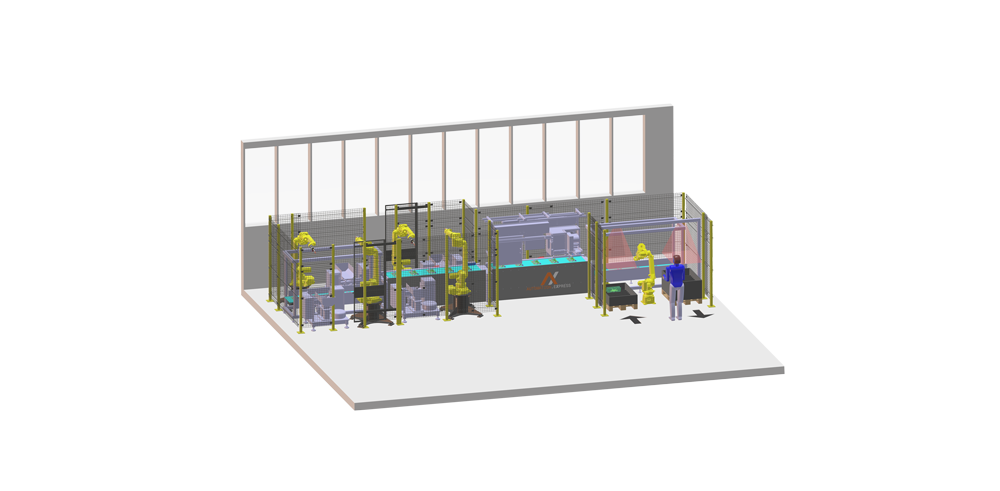
Nachher – vollautomatische Produktion
- Rohplatine wird über Palette im Beladebereich der Anlage bereitgestellt
- über 3D-Vision Sensor wird Rohplatine vom Roboter vom Beladebereich in die Montagelinie eingesteuert
- die vierfach Rohplatinen Aufnahme wird per Fördertechnik zum Montagestart transportiert
- in unterschiedlichen Stationen werden nun Schüttgut Montagebauteile für die Platine vereinzelt
- Roboter montiert vereinzelte Bauteile und dokumentiert Montageparameter je nach Variante
- in einer finalen Prüfanlage wird montierte Platine auf Funktion und Qualität geprüft
- nach der Prüfung entnimmt Roboter die IO-Platinen aus Aufnahme und legt diese in die Palette zurück; NIO Bauteil werden separiert
Sondermaschinen
automatische Schraubstation
mit vorgelagertem Bauteilscan
Leitsatz: bauteilflexible Spritzgussverschraubung
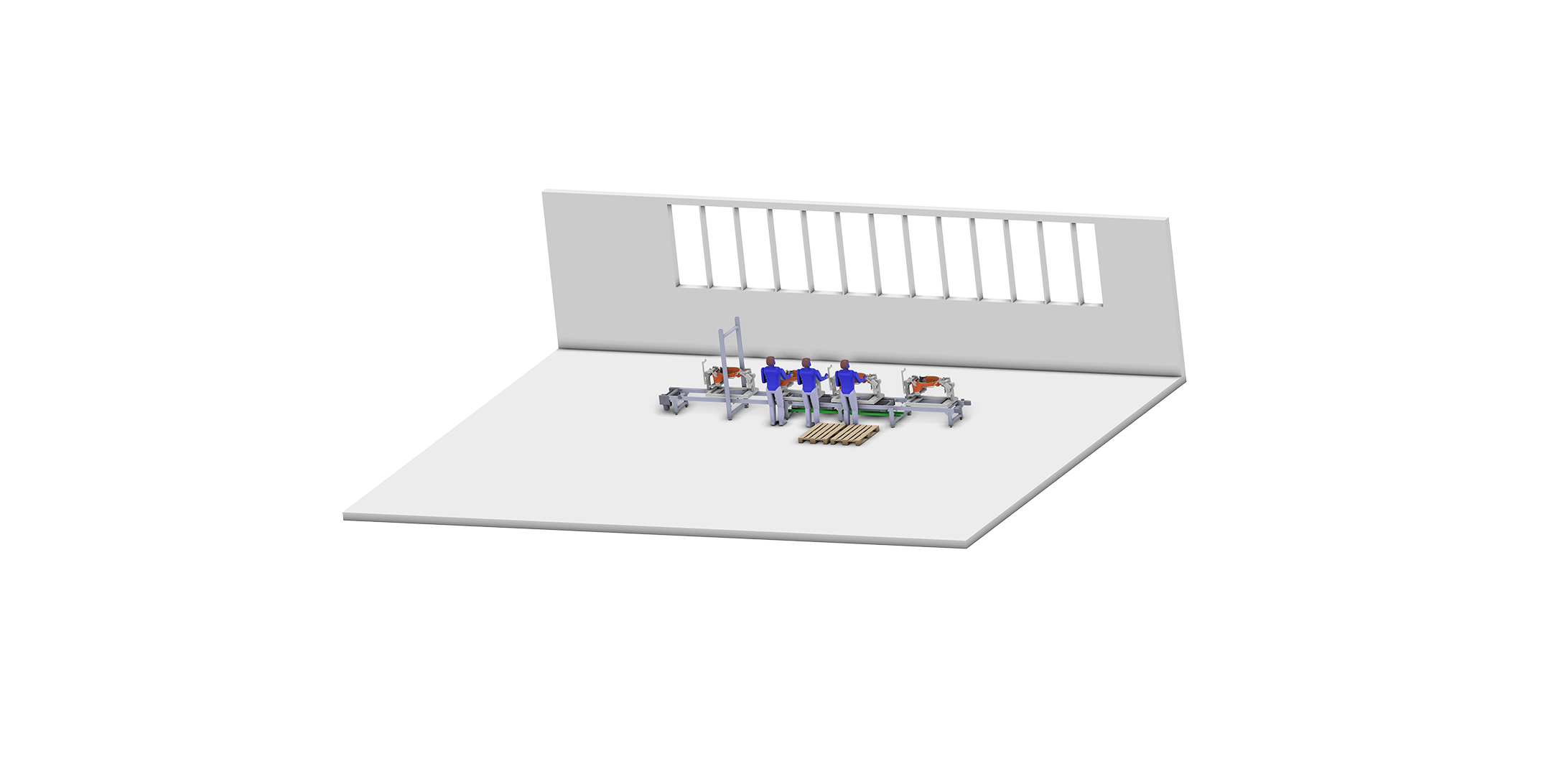
Vorher – manuelle Druckluftschrauber
- gesteckter Spritzguss-ZSB wird über eine Montagelinie transportiert
- Mitarbeiter fixieren Bauteile und verschrauben Spritzguss-ZSB mit verschiedenen Schraubtypen
- neues Bauteil wird im nachhinein montiert und ebenfalls verschraubt
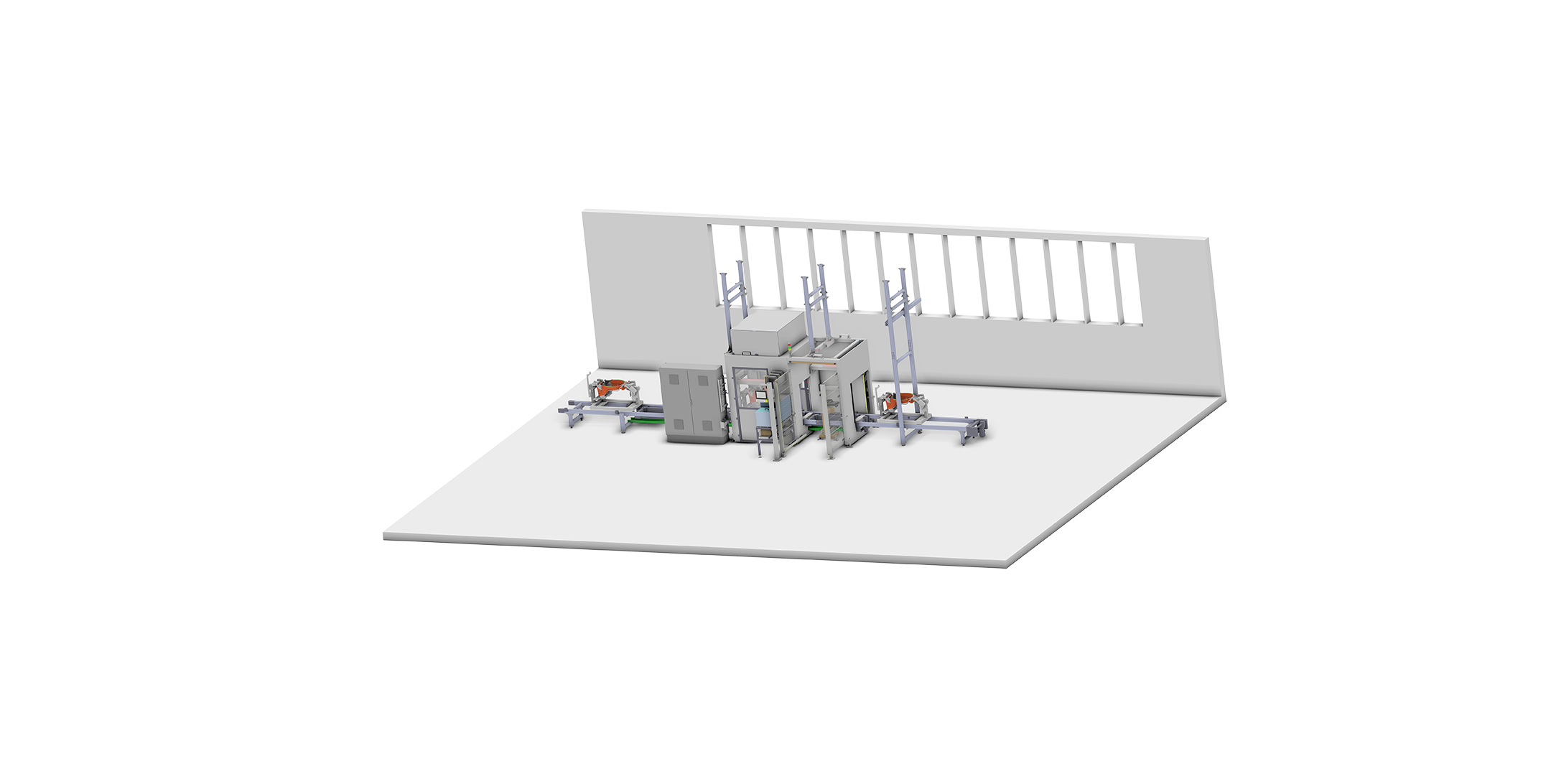
Nachher – Bauteilflexible Schraubstation
- gesteckter Spritzguss-ZSB wird über Montagelinie transportiert
- in Station1 wird Bauteil gescannt und Position der Schraubbohrungen ermittelt
- flexible Niederhalter halten ZSB in Form und automatische Schraubeinheiten verschrauben anhand Positionen vom Scan den Kunststoff-ZSB
- in Station 2 wird neues Bauteil hinzugefügt und ebenfalls verschraubt
- durch Bauteilscan können verschiedene ZSB-Varianten flexibel jederzeit verschraubt werden
vollautomatische 3D-Messzelle mit höchster Auflösung
und kurzer Taktzeit (<40sec pro Bauteil incl. Handling)
Leitsatz: modernste 3D-Messtechnologie automatisiert
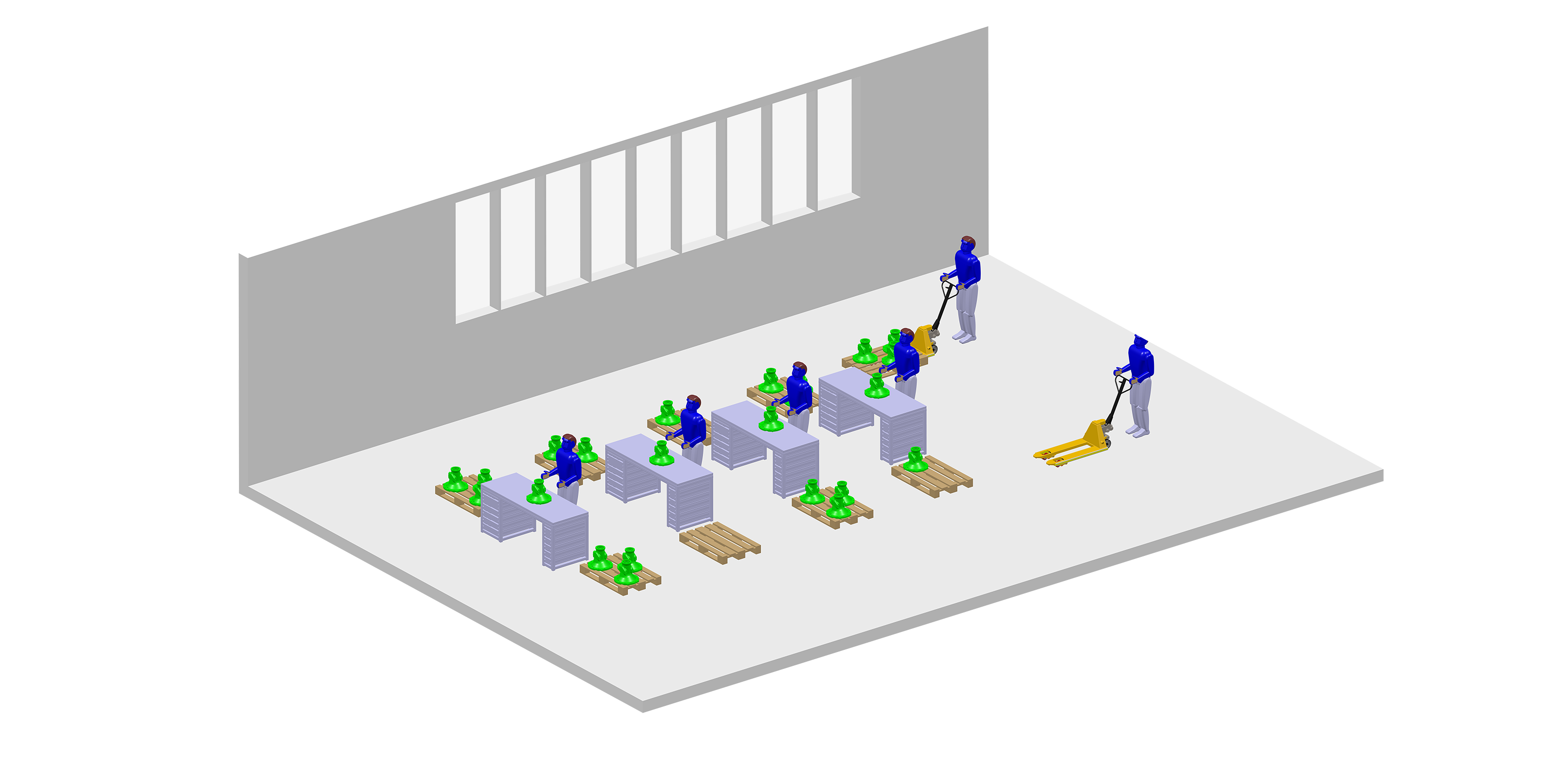
Vorher – manueller Prüfprozess
- Bauteile werden manuell durch Werker auf div. Merkmale (Beschädigungen, Geometrie,..) geprüft
- zur Geometrieprüfung werden Messlehren durch den Werker verwendet
- kein digitales Fehlerprotokoll bzw. vermerk Bauteil-ID zur Nachverfolgung und Auswertung
- keine prozessstabile Vollprüfung über die ganze Schicht durch Werker möglich
- unergonomische manuelle Bauteillogistik zu und vom Prüfplatz
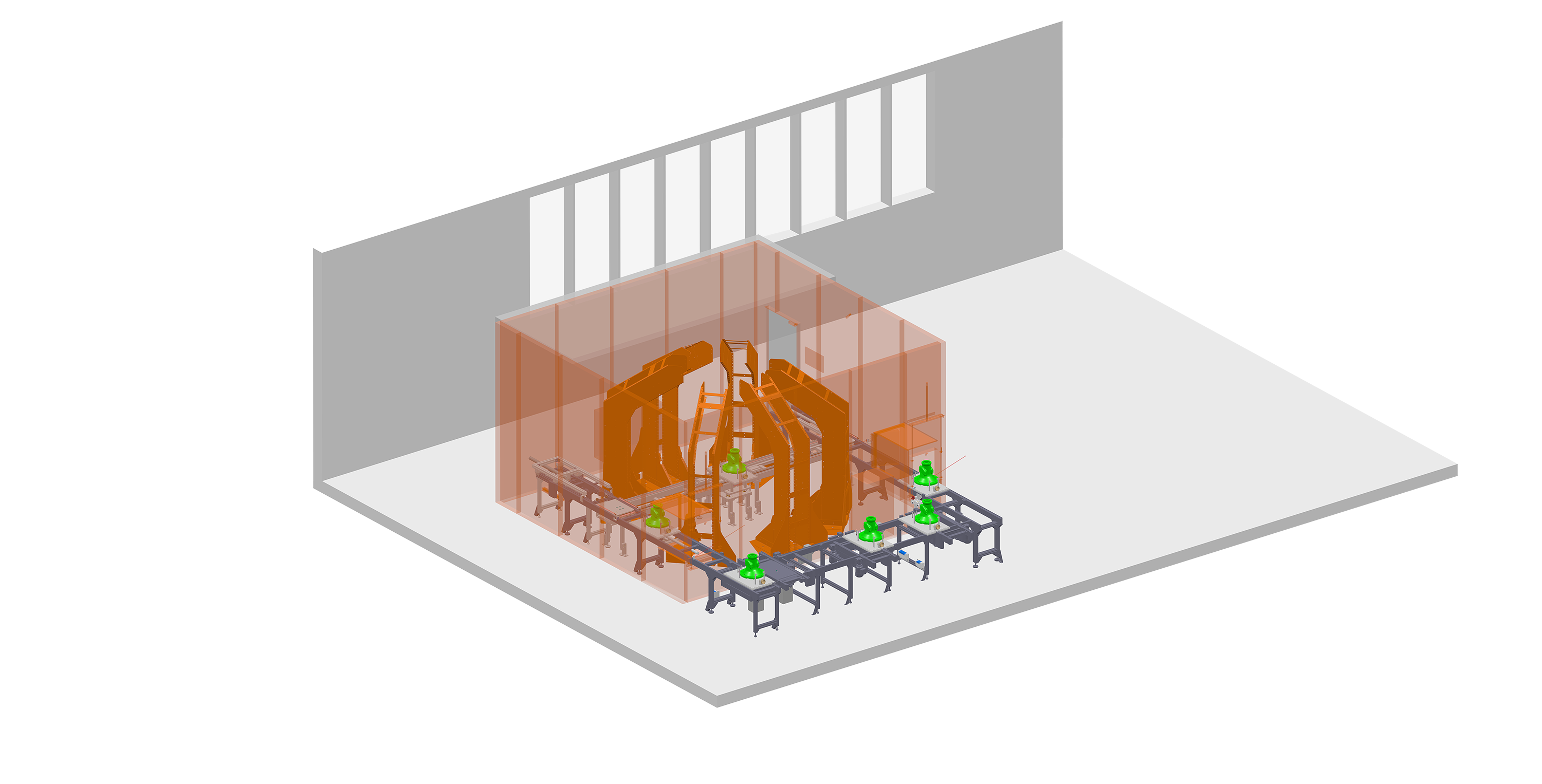
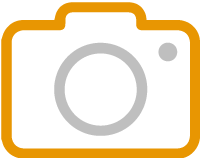
Nachher – automatisierte 3D-Messzelle
- automatisches Bauteilhandling ins Zentrum der Messzelle in 5sec
- Messung der Bauteile im 35 Sekunden Takt unabhängig von der Bauteilgeometrie
- durch 360° Grad Kameraanordnung, 3D-Punktewolke des gesamten Bauteils und Merkmalextraktion
- klimatisierte Messzelle mit Schleusentechnik für Fertigungsumgebungen
- keine Referenzmarken bzw. Vorbehandlung (Einsprühen) der Bauteil nötig
- vollautomatischer Kalibrierprozess integriert
Neuanlagentechnik
CNC Fertigungsanlage nach Kundenbedarf - Bohrautomat
Leitsatz: Robotik kommt zum Einsatz nur wo sinnvoll
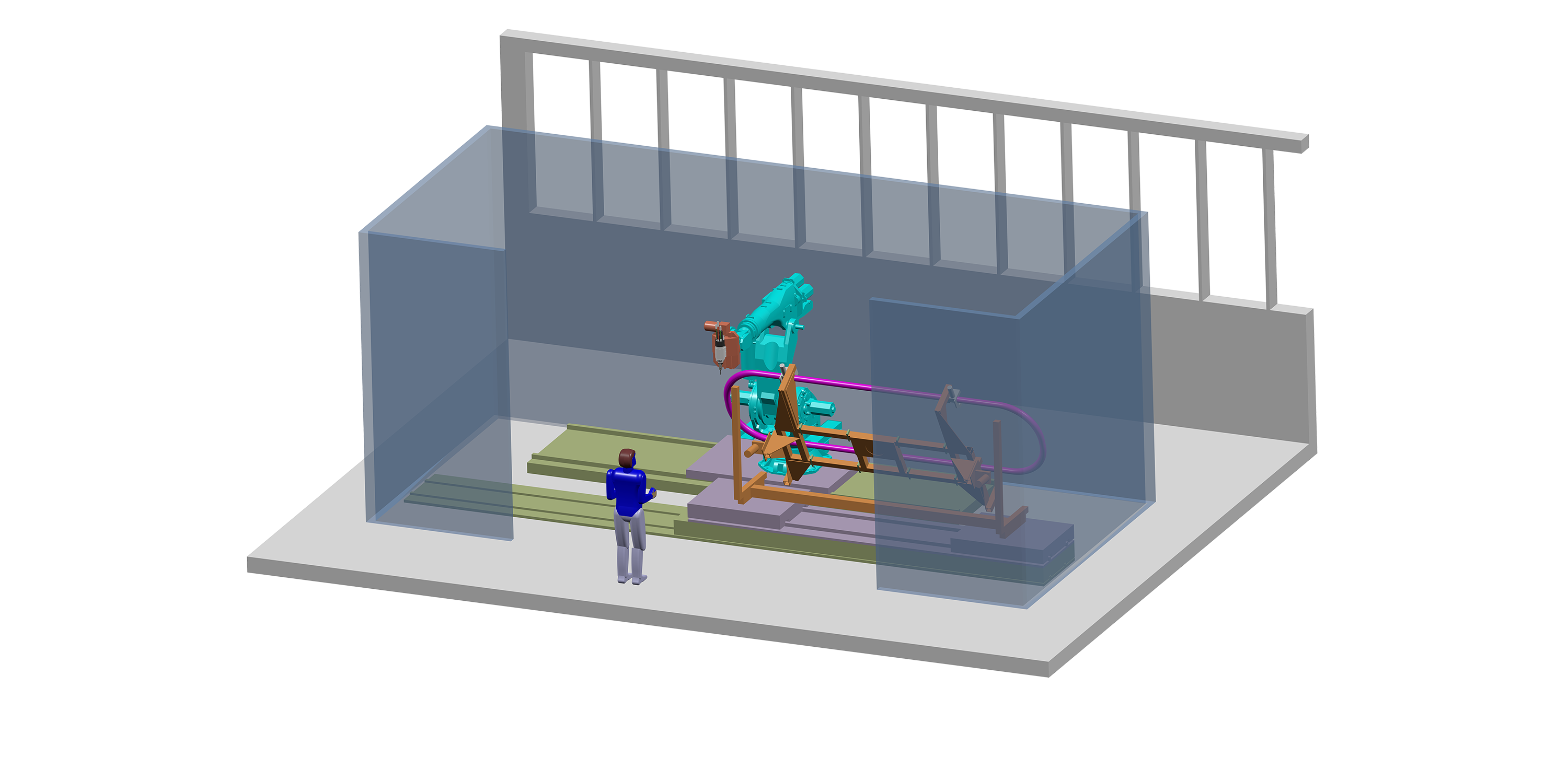
Vorher – Bohrspindel am Roboter
- durch Handlingsgewicht vom Roboter kleinere Spindelauswahl nötig
- kleinere Spindelauswahl = längere Prozesszeiten = reduziertes Drehmoment
- erhöhter Platzbedarf durch Verschieben des Produkts zur Erreichbarkeit aller Positionen
- 8Stk Achsen bis zur Spindel -> Stabilitätsverlust
- 3D Energieführung (Strom, Luft, Hydraulik, Kühlwasser,…) über Roboter zur Spindel -> Kabelbruch
- aufwendige Reinigung und Wartung der Anlage durch 3D-Manipulation der Spindel
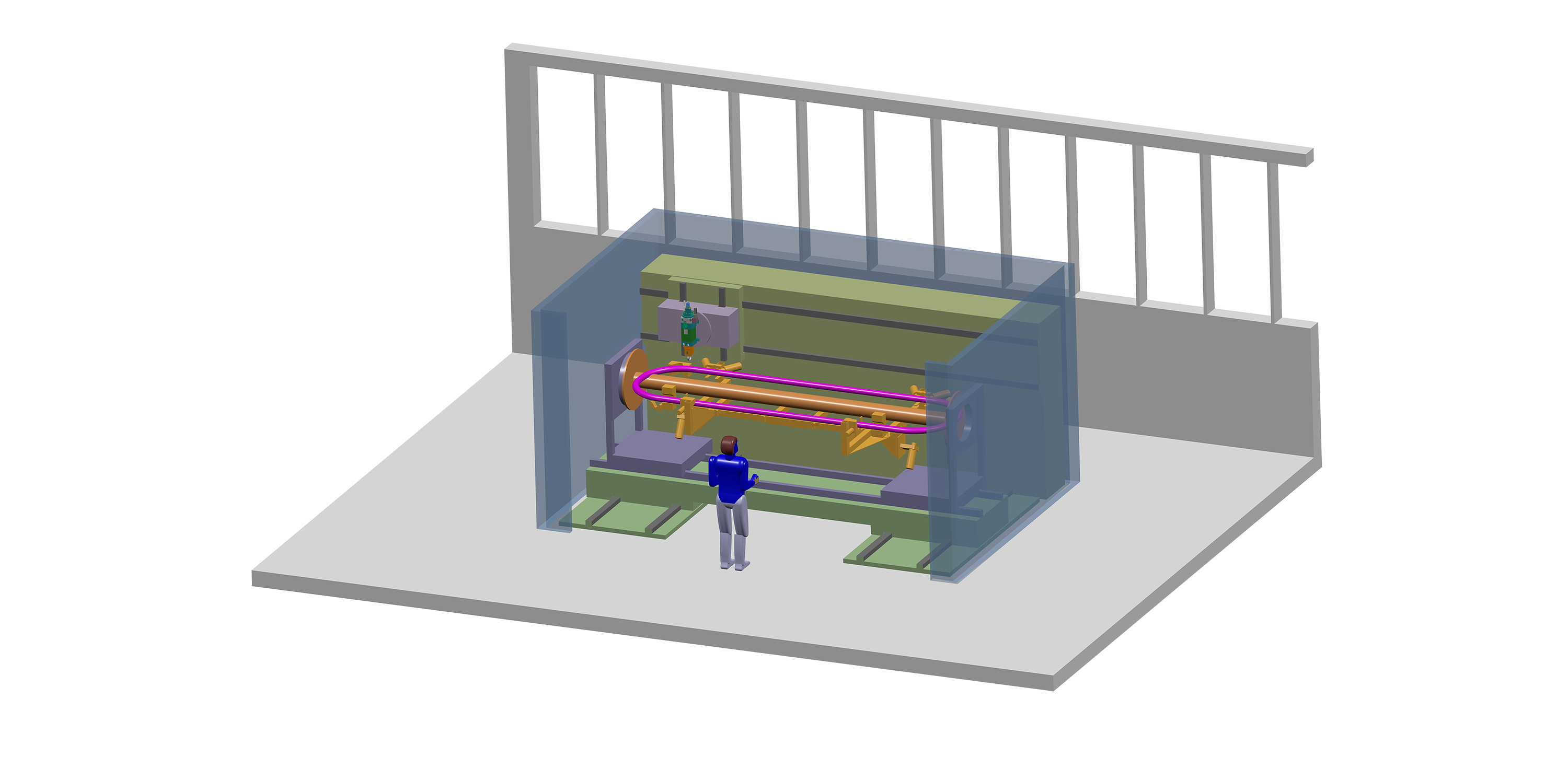
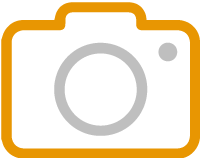
Nachher – Bohrspindel auf X,Y Positioniereinheit und einer Produktdrehachse
- Einsatz einer klassischen, leistungsstarken Industriespindel für Zerspanungsmaschinen
- optimale Spindelauswahl = verkürzte Prozesszeiten = hohes Drehmoment = HSK-A 63 Schnittstelle
- durch drehen des Produkt optimierter Platzbedarf (um 50% reduziert)
- 3Stk Achsen bis zur Spindel -> Prozessstabilität, Genauigkeit
- 2D Energieführung zur Spindel geschützt auf Rückseite der Anlage
- stationäre Bearbeitung mit darunterliegendem Späne- und Kühlmittelfang
spurgeführte Logistikplattform zur Verbindung
von Produktions- und Fertigungsprozessen
Leitsatz: automatisieren von monotonen Logistikprozessen
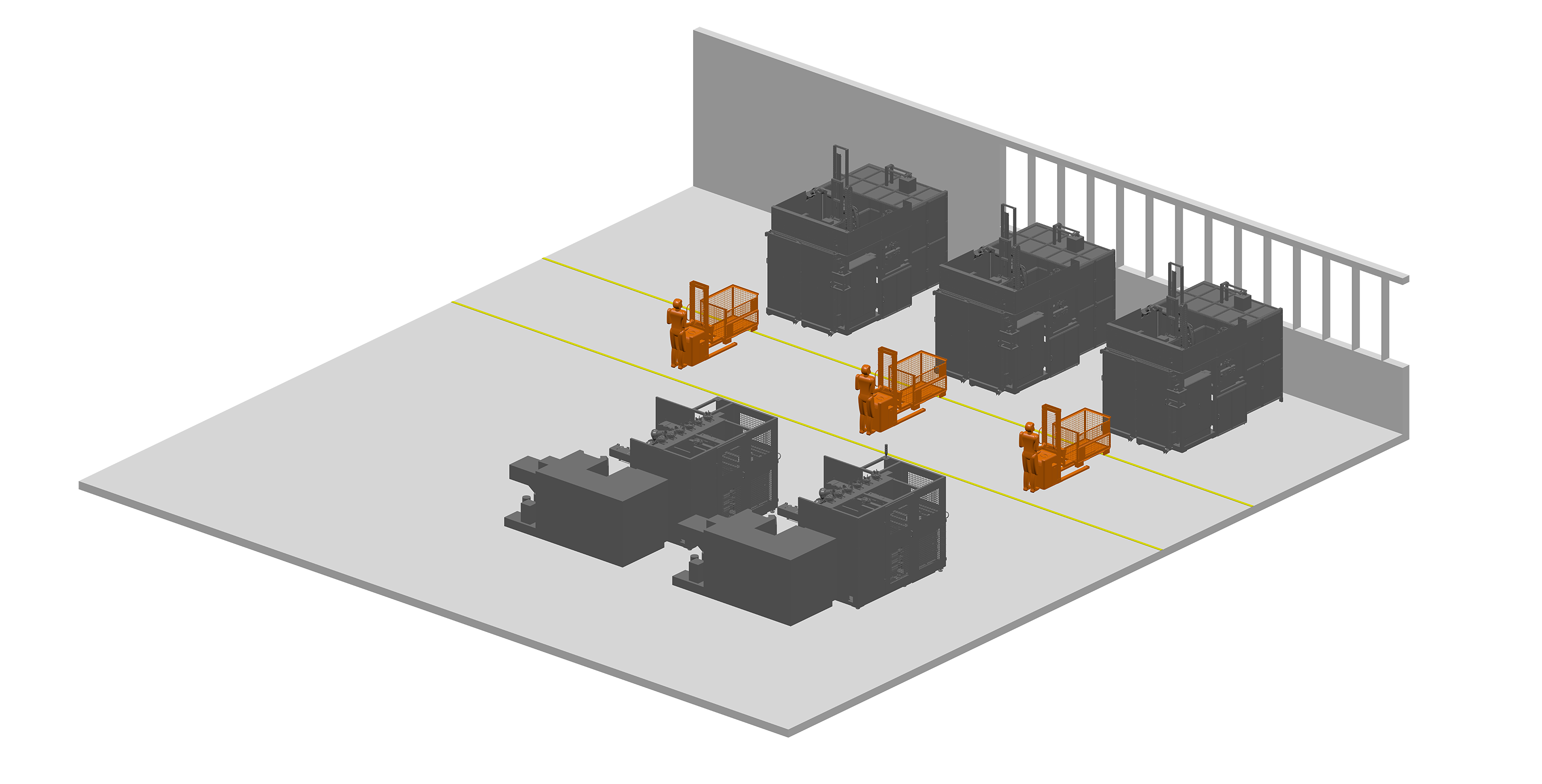
Vorher – manuelle Transportlogistik zwischen Produktionsanlagen
- Bauteilherstellung erfolgt über zwei, drei,.. getrennte Produktionsanlagen
- Bauteilpufferung je Anlage erfolgt über Ladeträger (z.b. Gitterbox, Paletten, usw. )
- Logistikprozess zwischen den Anlagen wird durch Mitarbeiter über Stapler, elektrischen Hubwagen oder dgl. durchgeführt
- leere Ladeträger müssen auch wieder manuell rückgeführt werden
- direkt Verbindung des Prozesses über Förderband aufgrund benötigter Barrierefreiheit für Staplerverkehr, Mitarbeitergehweg nicht möglich
- Produktionsflexibilität erlaubt keine direkte Verbindung aufgrund unterschiedlicher Taktzeitthematik
- Hängeförderer als Logistikverbindung zu großer Eingriff in die Infrastruktur
- für diesen simplen, direkten Logistikprozess ist der Einsatz von fahrerlosen Transportsysteme mit AMR-Technologie zu kosten- und wartungsintensiv
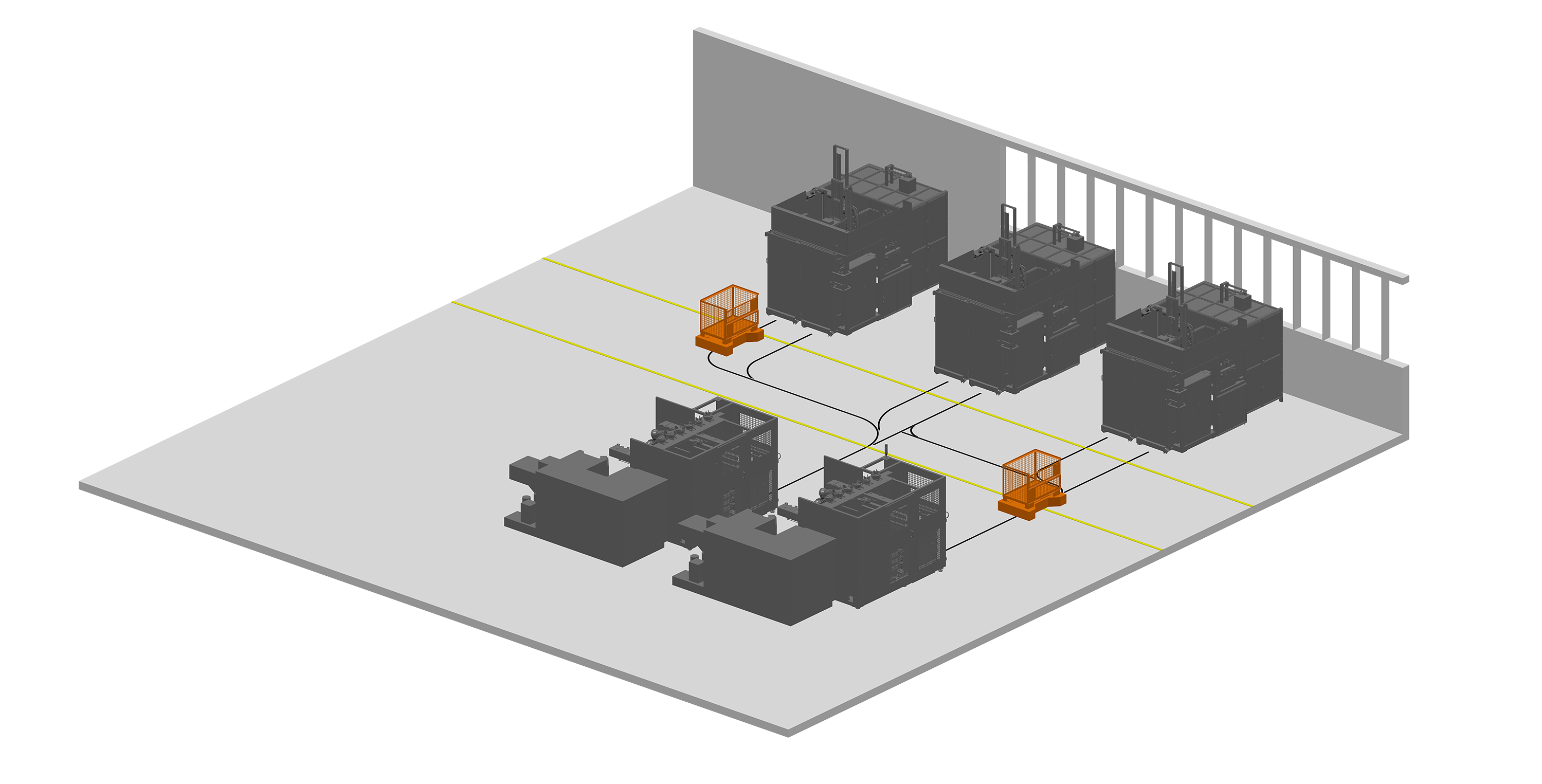
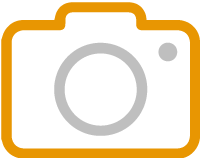
Nachher – Logistikprozess automatisiert
- einfache Logistikprozess zwischen den Anlagen wird über unsere spurgeführte Logistikplattform sichergestellt
- Steuerung der Logistikplattform erfolgt über eigene Siemens CPU und ist per W-LAN direkt mit den Produktionsanlagen verbunden
- über den Spurführungsassistent werden Weichen und individuelle Stopppositionen identifiziert bzw. die Spur bei beschädigtem oder verschmutztem Spurband gehalten
- über 360° Sicherheitstechnik werden Hindernisse detektiert, die Geschwindigkeit automatisch reduziert oder gestoppt und bei freier Fahrt wieder autark angefahren
- Be- und Entladung der Logistikplattform ist in den Produktionsanlagen integriert
- Dimensionierung der Zuladung, Größe nach Kundenwunsch möglich
- Logistikplattform kann auch als Baugruppenmontageplattform genutzt werden